To expand your news reach, consider advertising with our media partner, Patch Media, at https://heypapipromotionsmedia.town.news/. Patch is a nationwide news network comprising over 1,000 hyperlocal websites dedicated to community news across the United States. For press release distribution services, please call or visit https://heypapipromotions.com/advertise.
🌏 Blogs / Articles / News / Classifieds / Press Releases / PSA / Podcast / Poetry / Storytelling
Blogs (1492)
Automotive headlights are more than just functional components—they're a fusion of safety, style, and innovation. Whether illuminating a dark highway or accentuating a car's sleek design, headlights owe their precision and elegance to the molds that shape them. The automotive head light mold, often interchangeably referred to as the automotive head lamp mold, is the unsung hero behind these critical parts. But how exactly are these molds made?
1. The Blueprint Stage: Designing the Automotive Head Light Mold
Every automotive head light mold begins with a vision. Designers and engineers collaborate to create a headlight that not only looks striking but also meets stringent safety and performance standards. This initial stage is all about translating ideas into a workable design, and it's where creativity meets precision.
The process starts with conceptual sketches, often digitized into 3D models using software like CAD (Computer-Aided Design). These models map out every curve of the lens, the housing's contours, and even the mounting points that secure the headlight to the vehicle. The automotive head lamp mold must account for factors like light diffusion, material thickness, and thermal resistance, as headlights endure intense heat from bulbs or LEDs. Engineers also factor in a "draft angle"—a subtle taper that ensures the molded part can be removed without sticking.
Prototyping is a key part of this phase. Using 3D printing or small-scale molds, teams test their designs to catch flaws early. A lens with uneven clarity or a housing that warps under heat could spell disaster, so refining the automotive head light mold design here saves time and money down the line. By the end of this stage, the blueprint is ready—a digital masterpiece poised for physical creation.
2. Material Selection: Building a Durable Automotive Head Lamp Mold
Once the design is locked in, the focus shifts to the materials that will form the automotive head lamp mold. The mold itself isn't plastic like the headlight—it's typically crafted from metals like steel or aluminum, chosen for their strength and longevity. The material decision hinges on the production scale and complexity of the headlight design.
Steel is the go-to for high volume production. Its durability makes it ideal for an automotive head light mold that will churn out thousands of headlights without losing precision. Stainless or tool steel can withstand the heat and pressure of injection molding, ensuring consistent quality over countless cycles. For smaller runs or prototypes, aluminum offers a lighter, more affordable alternative. It's easier to machine and cools faster, speeding up the manufacturing process.
The choice also depends on the headlight's material—usually polycarbonate or acrylic for their clarity and toughness. The automotive head lamp mold must be compatible with these plastics, resisting wear from repeated injections while maintaining a flawless surface. Polishing the mold to a mirror finish is often a final touch, especially for transparent lenses, as any imperfection transfers directly to the headlight.
3. Crafting the Mold: Precision Manufacturing Techniques
With materials selected, it's time to bring the automotive head light mold into existence. This is where advanced manufacturing techniques shine, turning a block of metal into a precision tool. The process is both an art and a science, demanding accuracy down to the micrometer.
CNC (Computer Numerical Control) machining is the backbone of mold creation. Guided by the 3D design, CNC machines carve the steel or aluminum block into the exact shape of the headlight's negative space. This might involve milling cavities for the lens and housing, drilling channels for cooling, or cutting slots for ejector pins. For intricate details—like the tiny prisms that scatter light in a headlight lens—EDM (Electrical Discharge Machining) steps in. EDM uses electrical sparks to erode metal with pinpoint precision, perfect for complex automotive head lamp mold features.
After machining, the mold undergoes finishing. Surfaces are polished to eliminate roughness, and critical areas are inspected for tolerances. A single flaw in the automotive head light mold could lead to defects like air bubbles or uneven edges in the final headlight. Once perfected, the mold is assembled—often in two halves that clamp together during production—and prepared for its starring role on the factory floor.
4. The Molding Process: From Mold to Headlight
The true test of an automotive head lamp mold comes during production, where it transforms raw materials into finished headlights. Injection molding is the dominant method, a high-pressure dance of heat, plastic, and timing that brings the mold's design to life.
The process begins with the automotive head light mold mounted in an injection molding machine. Pellets of polycarbonate or acrylic are heated until molten, then injected into the mold's cavity at pressures that can exceed 20,000 PSI. This force ensures the material fills every nook, from the lens's subtle curves to the housing's mounting tabs. Cooling follows, often accelerated by water channels built into the mold, solidifying the plastic into its final shape. After a brief pause—sometimes just seconds—the mold opens, and the headlight pops out.
Quality is king here. Each part is checked for defects: a lens with cloudiness could reduce visibility, while a warped housing might not fit the car. The automotive head lamp mold must perform reliably, cycle after cycle, to meet demand without compromising standards. Adjustments—like tweaking injection speed or cooling time—fine-tune the process, ensuring every headlight is road-ready.
5. Innovations and the Future of Automotive Head Light Molds
The manufacturing process for an automotive head light mold isn't static—it evolves with the industry. Today's headlights are smaller and smarter, thanks to LED technology and adaptive systems that adjust beams on the fly. These advancements demand molds with tighter tolerances and integrated features, like slots for sensors or hinges for moving parts.
Sustainability is also reshaping the landscape. Manufacturers are experimenting with recycled plastics and bio-based materials, which behave differently under heat and pressure. Crafting an automotive head lamp mold that handles these eco-friendly options requires innovation in design and machining. Meanwhile, emerging technologies like 4D printing—where materials adapt post-production—could revolutionize how molds are made, potentially allowing them to self-adjust during use.
For those in the field, mastering the automotive head light mold process means staying ahead of these trends. It's a craft that balances tradition with progress, ensuring headlights remain both functional marvels and design icons.
The manufacturing process of an automotive head light mold—or automotive head lamp mold—is a journey of precision and ingenuity. From the spark of design to the final molded headlight, every step reflects a commitment to quality and performance. As cars evolve, so will the molds that shape their lights, blending cutting-edge tech with timeless craftsmanship. Next time you flick on your headlights, spare a thought for the intricate process behind them—a hidden masterpiece lighting the way forward.
One of a mold manufacturers in china here! Younger Mould is a renowned mold manufacturer in china, recognized for its outstanding reputation and trusted position in the industry. We have earned the trust and praise of countless customers through our commitment to quality and innovation. If you're interested in our automotive head lamp mold, feel free to leave your contact information. Our team will provide you with competitive quotations and exceptional service tailored to your needs.
An AL159594 wheel hub seal is a critical component in a tractor's wheel assembly, designed to prevent contaminants such as dirt, dust, and moisture from entering the wheel bearings. It also helps to retain lubrication inside the wheel bearing hub, ensuring smooth operation and reducing friction.
The AL159594 wheel bearing hub seal is typically made of high quality rubber or metal and is strategically placed within the wheel hub assembly. This seal plays an essential role in maintaining the longevity and efficiency of the wheel bearings by preventing grease or oil leaks. A failing wheel hub oil seal can lead to severe mechanical issues, including premature wear of the wheel bearings and increased safety risks while driving.
What Should a Wheel Hub Seal Be Checked For?
Regular inspection of a AL159594 wheel hub seal is crucial for maintaining the performance and safety of a vehicle. Here are the primary factors to check:
1. Oil or Grease Leaks
A visible sign of a wheel hub oil seal failure is the presence of oil or grease around the hub area. This indicates that the seal is no longer providing proper containment.
2. Excessive Wear or Cracks
Inspecting the wheel bearing hub seal for cracks, tears, or general deterioration can help prevent unexpected failures.
3. Contaminant Buildup
A broken or worn out seal allows debris, water, and dirt to enter the hub, which can lead to rust, corrosion, and bearing damage.
4. Unusual Noises from the Wheel Area
A grinding or humming sound while driving could indicate insufficient lubrication due to a leaking wheel hub seal.
5. Uneven Tire Wear
Leaking oil can affect the wheel's alignment and result in uneven tire wear, reducing tire lifespan and affecting vehicle handling.
How Long Can You Drive with a Leaking Wheel Hub Seal?
Driving with a leaking wheel hub oil seal is not advisable, as it can lead to severe mechanical issues and safety hazards. However, the time before a critical failure depends on several factors, including the severity of the leak and driving conditions.
Minor Leaks: If the leak is small, it may be possible to drive for a short period before major damage occurs. However, it is best to address the issue as soon as possible to avoid costly repairs.
Moderate Leaks: When a leak is noticeable but not yet critical, driving for extended periods can cause wheel bearings to overheat and fail.
Severe Leaks: If significant oil loss occurs, it can lead to immediate wheel bearing damage, increasing the risk of wheel detachment or brake failure. In this case, the vehicle should not be driven.
Risks of Driving with a Leaking Wheel Hub Seal:
Increased friction and overheating of wheel bearings
Possible loss of wheel functionality
Higher repair costs due to additional component damage
Reduced vehicle control and braking efficiency
If you notice a wheel hub seal leak, it is best to repair or replace the seal immediately to prevent further complications.
Is a Leaking Wheel Hub Seal a DOT Violation?
Yes, a leaking wheel hub seal can be considered a DOT (Department of Transportation) violation, especially in commercial vehicles such as trucks and buses. According to DOT regulations, vehicle inspections require that wheel seals be free from leaks to ensure road safety.
DOT Compliance Factors:
Visible Leaks: Any visible leakage around the wheel hub could result in a failed inspection.
Brake Contamination: If oil or grease leaks onto the brake components, it can reduce braking efficiency, leading to safety violations.
Excessive Bearing Wear: Damaged seals that allow dirt and moisture to enter the hub can lead to bearing failure, increasing the risk of accidents.
Consequences of a DOT Violation:
Potential fines or penalties
Vehicle being taken out of service until repaired
Increased maintenance and repair costs
To avoid a DOT violation, regular maintenance and prompt replacement of a failing wheel hub oil seal are essential.
What's Involved in Replacing a Wheel Hub Seal?
Replacing a wheel hub seal involves several steps and requires proper tools and expertise. While some experienced vehicle owners may attempt a DIY replacement, professional service is recommended to ensure safety and reliability.
Steps to Replace an AL159594 Wheel Hub Seal:
Lift and Secure the Vehicle
Use a jack to lift the vehicle and secure it with jack stands.
Remove the Wheel and Brake Components
Take off the wheel, brake caliper, and rotor to access the wheel hub assembly.
Detach the Hub Assembly
Unbolt and remove the wheel hub to reach the old seal.
Extract the Old Seal
Use a seal removal tool to carefully pry out the damaged wheel bearing hub seal.
Clean and Inspect Components
Ensure the wheel bearings and hub are free from contaminants or damage before installing a new seal.
Install the New Seal
Press the new AL159594 wheel hub oil seal into place, ensuring a secure and proper fit.
Reassemble the Components
Reattach the hub, rotor, brake components, and wheel.
Test for Leaks and Proper Functioning
After installation, check for leaks and ensure the wheel spins freely before lowering the vehicle.
Cost of Replacement:
DIY Replacement: $30 - $80 for the seal and necessary tools.
Professional Service: $200 - $500, depending on the vehicle type and labor costs.
While it may be tempting to postpone replacing a wheel hub oil seal, timely maintenance can prevent costly repairs and safety risks.
A wheel hub seal leak is a serious issue that should not be ignored. It can lead to wheel bearing failure, reduced vehicle performance, and potential safety hazards. Ignoring a leaking wheel bearing hub seal can also result in DOT violations, fines, and vehicle downtime.
Regular inspection and prompt replacement of a wheel hub oil seal can help maintain vehicle safety, extend the lifespan of wheel components, and ensure compliance with road safety regulations. If you suspect a leak, addressing it immediately will save you time, money, and potential safety risks in the long run.
High quality wheel hub seal for sale! Choose from our extensive line of AL159594 wheel hub oil seal for JD tractor, crafted by CXNOFIA, a reputable Chinese tractor parts for JD manufacturer. Enjoy top quality wheel bearing hub seal at competitive prices, quick international shipping, convenient returns, and limited time deals!
In the world of laboratory research, the proper storage and handling of reagents are crucial for maintaining the integrity of experiments and ensuring accurate results. One essential tool that has stood the test of time is the screw cap reagent bottle. These bottles are designed to provide a secure, reliable, and convenient solution for storing and managing various chemicals, solvents, and reagents. Whether you are working in a chemistry lab, a pharmaceutical facility, or any other scientific environment, understanding the benefits and proper use of screw cap reagent bottles can significantly enhance your laboratory operations.
A screw cap reagent bottle is a versatile container specifically designed to hold and preserve reagents. These bottles come in various sizes and materials to cater to different laboratory needs. One of the most popular types is the wide mouth reagent bottle with a screw cap. The wide mouth design allows for easy access and pouring of reagents, while the screw cap ensures a tight seal to prevent spills, evaporation, and contamination.
The function of a screw cap reagent bottle is not only to store chemicals safely but also to provide a user friendly solution for laboratory personnel. The screw cap mechanism allows for easy opening and closing, ensuring that the reagent remains uncontaminated and stable during storage. Additionally, the wide mouth design facilitates the addition of solid or powdered reagents, making it an ideal choice for a variety of laboratory applications.
Benefits of Screw Cap Reagent Bottles
Screw cap reagent bottles offer numerous advantages over other types of containers, making them a preferred choice in laboratories worldwide. Here are some key benefits:
1. Secure Sealing and Leak Prevention
One of the most significant advantages of screw cap reagent bottles is their ability to provide a tight and secure seal. The screw cap mechanism ensures that the bottle remains tightly closed, preventing leaks and spills. This is particularly important when handling hazardous chemicals or volatile solvents, as it helps maintain laboratory safety and prevents contamination of other samples.
2. Ease of Use and Accessibility
Wide mouth reagent bottles with screw caps are designed for user convenience. The wide opening allows for easy pouring and dispensing of liquids, as well as the addition of solid or powdered reagents. This design reduces the risk of spills and makes it easier for laboratory personnel to handle the contents without compromising safety.
3. Durability and Versatility
Screw cap reagent bottles are typically made from high-quality materials such as glass or durable plastics, ensuring their longevity and resistance to chemical corrosion. These materials are designed to withstand the harsh conditions of a laboratory environment, making them suitable for storing a wide range of reagents, from acids and bases to organic solvents.
4. Customization and Labeling
Many screw cap reagent bottles come with customizable features such as labeling areas or color coded caps. This allows laboratory personnel to easily identify the contents of each bottle, reducing the risk of mix ups and ensuring proper documentation and traceability.
5. Cost Effective and Space Saving
Screw cap reagent bottles are often available in bulk from specialized factories, making them a cost effective solution for laboratories with high storage needs. Additionally, their compact design allows for efficient storage in laboratory cabinets or on shelves, maximizing the use of available space.
Choosing the Right Screw Cap Reagent Bottle
When selecting a screw cap reagent bottle for your laboratory, several factors should be considered to ensure that you choose the right product for your specific needs.
1. Material Selection
Reagent bottle screw cap is commonly made from two main materials: glass and plastic. Glass bottles are ideal for storing highly reactive chemicals or those that require precise temperature control, as glass is inert and has excellent chemical resistance. However, glass bottles are also more fragile and can break if dropped.
Plastic reagent bottles, on the other hand, are more durable and lightweight. They are suitable for storing a wide range of reagents, including solvents and non reactive chemicals. Common plastic materials used for reagent bottles include polyethylene (PE) and polypropylene (PP), which offer good chemical resistance and are less likely to break.
2. Size and Capacity
Reagent bottle screw cap comes in various sizes, ranging from small vials to larger containers. The size you choose will depend on the volume of reagent you need to store. For example, a wide mouth reagent bottle with a screw cap is ideal for storing larger quantities of reagents, while smaller bottles are suitable for storing more concentrated or expensive chemicals.
3. Cap Design
The cap design is another important consideration. Screw caps are available in different styles, such as standard caps, tamper evident caps, and caps with built in droppers or pour spouts. Choose a cap design that best suits your laboratory's needs and the specific reagents you will be storing.
4. Quality and Compliance
Ensure that the reagent bottles you choose meet the required standards and certifications for laboratory use. Look for products that comply with industry standards such as ASTM or ISO, and consider purchasing from reputable manufacturers or factories that specialize in laboratory supplies.
Proper Use and Handling of Screw Cap Reagent Bottles
To maximize the benefits of screw cap reagent bottles and ensure laboratory safety, it is essential to follow proper use and handling procedures.
1. Storage Conditions
Store reagent bottles in a cool, dry, and well-ventilated area away from direct sunlight. Ensure that the bottles are tightly sealed with the screw cap to prevent evaporation or contamination. Keep hazardous chemicals separate from other reagents to avoid cross-contamination.
2. Labeling and Documentation
Always label your reagent bottles clearly with the name of the reagent, concentration, date of storage, and any relevant hazard symbols. Proper labeling is crucial for maintaining laboratory safety and ensuring that the correct reagent is used in experiments.
3. Opening and Closing
When opening a screw cap reagent bottle, use a gentle twisting motion to avoid applying excessive force, which could damage the cap or bottle. Close the bottle tightly after each use to maintain the integrity of the reagent and prevent spills.
4. Dispensing Reagents
When dispensing reagents from a wide mouth bottle, use a clean spatula or scoop for solids, or a pipette for liquids. Avoid touching the inside of the bottle or the cap with your hands to prevent contamination. Always replace the screw cap immediately after dispensing.
5. Cleaning and Maintenance
Regularly clean your reagent bottles to remove any residual chemicals or contaminants. Use a mild detergent and water, and ensure that the bottles are thoroughly rinsed and dried before reuse. Inspect the screw caps for any signs of wear or damage, and replace them if necessary.
Sourcing High Quality Screw Cap Reagent Bottles
Finding a reliable supplier for screw cap reagent bottles is crucial for maintaining laboratory efficiency and safety. Many specialized factories offer a wide range of reagent bottles with screw caps, catering to different laboratory needs. When sourcing your reagent bottles, consider the following:
1. Manufacturer Reputation
Choose a reputable manufacturer with a proven track record of producing high-quality laboratory supplies. Look for customer reviews and testimonials to ensure that the products meet industry standards and are reliable.
2. Customization Options
Select a factory that offers customization options, such as different bottle sizes, cap designs, and labeling features. This allows you to tailor your reagent bottles to your specific laboratory requirements.
3. Quality Assurance
Ensure that the manufacturer follows strict quality control measures and complies with relevant industry standards. This guarantees that the reagent bottles you purchase are safe, durable, and suitable for laboratory use.
4. Customer Support
Choose a supplier that provides excellent customer support, including technical assistance, product information, and after-sales service. This ensures that you can address any issues or concerns promptly and receive guidance on proper use and maintenance.
Screw cap reagent bottles are an essential tool in any laboratory, providing a secure, reliable, and user-friendly solution for storing and managing reagents. By understanding the benefits of these bottles, selecting the right product for your needs, and following proper use and handling procedures, you can enhance laboratory efficiency, safety, and accuracy.
Whether you are purchasing wide mouth reagent bottles with screw caps from a specialized factory or simply updating your laboratory's storage solutions, always prioritize quality, durability, and compliance. With the right screw cap reagent bottles, you can ensure that your laboratory operations run smoothly and that your reagents remain safe and stable.
Invest in high quality screw cap reagent bottles today, and experience the difference they can make in your laboratory's performance and safety.
Yongkang Medical is a renowned wide mouth reagent bottle with screw cap factory of premium quality screw cap reagent bottle. We specialize in creating and producing reagent bottle screw cap that are tailored to meet the diverse needs of our clients while surpassing their expectations. For inquiries or to purchase, feel free to contact us at: czyk001@163.com or eric@yongkangcn.com.
When it comes to home hardware, the smallest details can make a big impact. Take door stoppers, for example—they're often overlooked, yet they play a crucial role in protecting your walls, doors, and peace of mind. Among the many options out there, the zinc alloy door stopper has gained attention for its durability and style. But is it really any good? How does it stack up against alternatives like a solid rubber door stop or a metal door blocker?
What Makes Zinc Alloy Door Stoppers Stand Out?
Let's start with the basics: what exactly is a zinc alloy door stopper? Zinc alloy is a blend of zinc with other metals like aluminum, copper, or magnesium, creating a material that's strong, versatile, and resistant to wear. Unlike pure zinc, the alloyed version doesn't corrode easily, making it a reliable choice for hardware like door stoppers.
A zinc alloy door stopper typically comes in forms like a cylindrical door stopper or a wall mounted design, often paired with a solid rubber tip to cushion the door's impact. Its appeal lies in its combination of strength and aesthetics. Available in finishes like satin chrome, brushed nickel, or antique brass, it can blend seamlessly into your decor—whether you're outfitting a modern kitchen or a cozy bedroom.
Compared to a solid rubber door stop, which is purely functional and often temporary, or a heavy metal door blocker, which prioritizes brute force over finesse, the zinc alloy stopper strikes a balance. It's sturdy enough to handle daily use but light enough to install without fuss. Plus, its smooth surface resists rust and yellowing, promising longevity—a big win for anyone tired of replacing flimsy plastic stoppers.
How Does a Zinc Alloy Door Stopper Perform?
Performance is where the rubber meets the road—or in this case, where the door meets the stopper. A zinc alloy door stopper shines in several key areas:
Durability: Thanks to its metal composition, it holds its shape under pressure. Whether it's a lightweight interior door or a heavier exterior one, a cylindrical door stopper made of zinc alloy can take the hit without bending or cracking. Unlike a solid rubber door stop that might wear down or tear over time, zinc alloy keeps going strong.
Impact Resistance: Paired with a solid rubber tip, it absorbs shock effectively. This is a step up from a basic metal door blocker, which might dent a door or wall without that cushioning. The rubber component also quiets the impact—no more startling bangs when the kids swing the door open.
Stability: Floor mounted zinc alloy door stoppers, like the cylindrical variety, stay put. Their solid construction means they won't slide around like a lightweight rubber wedge might on slick floors. For heavier doors, a metal door blocker might edge out in sheer stopping power, but zinc alloy offers plenty for most homes.
That said, it's not perfect. If your door is unusually heavy—like a solid oak entryway—a zinc alloy stopper might need backup from a heftier metal door blocker. And while it resists rust, extreme humidity could eventually tarnish cheaper models. Overall, though, its performance makes it a contender for everyday use.
Installation and Practicality: Easy or a Hassle?
One of the big questions about any door stopper is how easy it is to get in place. A zinc alloy door stopper scores high here, especially compared to alternatives.
Mounting Options: You'll find zinc alloy stoppers in floor-mounted designs (like the cylindrical door stopper) or wall-mounted versions. Installation is straightforward: a few screws, a drill, and you're set. For a floor model, you'll secure it where the door swings; for a wall stopper, it goes where the knob would hit. Contrast this with a solid rubber door stop—no tools needed, just wedge it under the door—but also no permanence.
Tools and Time: Installing a zinc alloy door stopper takes 10–15 minutes per unit. You'll need a screwdriver and maybe a drill if your floor or wall isn't prepped. A metal door blocker might demand more muscle (and heavier anchors), while a rubber stop skips the hassle entirely—at the cost of stability.
Versatility: It works on wood, tile, or carpet, adapting to most home surfaces. The rubber tip prevents scratches, a perk over some metal door blockers that might scuff delicate floors.
The trade off? It's not as portable as a solid rubber door stop you can toss wherever needed. Once installed, it's fixed—great for consistent use, less so if you like flexibility. Still, for a semi permanent solution that looks good and performs well, zinc alloy is tough to beat.
Aesthetics and Value: Does It Look Good and Last?
Let's be honest—function matters, but so does style. A zinc alloy door stopper brings a polished vibe that elevates it above basic options.
Design Appeal: Whether it's a sleek cylindrical door stopper or a sculpted wall mount, zinc alloy comes in finishes that complement your hardware—think matte black for a modern edge or antique copper for vintage charm. A solid rubber door stop, while practical, rarely wins style points, and a metal door blocker can feel clunky or industrial.
Longevity: That rust-resistant surface means it won't fade or corrode quickly, even in damp areas like bathrooms. Compare that to a rubber stop that cracks after months of use or a painted metal blocker that chips over time—zinc alloy holds its own.
Cost vs. Benefit: Priced between $5–$15 per unit, it's more than a cheap rubber wedge but less than a premium metal door blocker. You're paying for durability and looks, and for many, that's worth it. A well-made zinc alloy door stopper can last years, saving you from frequent replacements.
The downside? If your decor leans ultra-minimalist, its metallic sheen might stand out too much. And while it's affordable, it's not the budget king—a pack of rubber stops costs less upfront. But for a blend of form and function, it's a solid investment.
Should You Get a Zinc Alloy Door Stopper?
After weighing the pros and cons, the answer is clear: yes, a zinc alloy door stopper is good—really good—for the right situation. It's durable enough to handle years of door swings, stylish enough to blend into your decor, and practical enough to install without a headache. Whether you pick a cylindrical door stopper or a wall-mounted version, its mix of zinc alloy strength and solid rubber cushioning makes it a standout.
Sure, it's not the cheapest option (hello, solid rubber door stop) or the toughest (step aside, metal door blocker), but it doesn't need to be. For homeowners wanting a balance of performance, longevity, and looks, it's a winner. Next time your door bangs the wall, think about swapping that old wedge for a zinc alloy door stopper. Your walls—and your ears—will thank you. Ready to give it a try?
Discover our premium selection of 9012 cylindrical door stopper form Filta. Ready to enhance your home with the convenience of metal door blocker? Visit Filta today and unlock a world of possibilities. Your ideal Filta hardware is just a click away!
The scripture tells us that the peace of God exceeds anything we can understand. But we can't experience that peace unless we have peace with God. How do we get peace with God? Click on the link below to read today's post and find out. #BibleStudy #Devotions #Evangelism #Romans
Standard Bullet Resistant Doors
What's the Common Materials Used?
Ballistic Steel: A primary component of standard bullet-resistant doors, ballistic steel is designed to withstand the impact of bullets. It is durable, tough, and highly resistant to penetration.
Fiberglass and Kevlar: These materials are often used in combination with steel to provide additional strength and energy absorption. Kevlar, in particular, is known for its high tensile strength and is frequently layered to improve the door’s protective capabilities.
Polycarbonate or Acrylic Panels: Some standard doors may also feature bullet-resistant glass or transparent polycarbonate for visibility, ensuring that the door still provides protection without completely obstructing the view.
What's the Protection Level?
- Level 2: Provides protection against 9mm or .357 Magnum rounds, offering higher protection.
- Level 3: Designed to withstand more powerful handgun ammunition like .44 Magnum or .357 Sig.
What's the Use Cases?
Standard bullet-resistant doors are ideal for environments where security is important but where extreme levels of ballistic resistance are not necessary. Common use cases include:
2. Retail Stores: Particularly in high-crime areas, these doors provide additional security for storefronts or back rooms.
3. Government Offices: In regions with moderate threat levels, these doors offer basic protection against armed intruders.
4. Residential Properties: Homeowners in high-risk neighborhoods can benefit from the added security of a standard bullet-resistant door without the need for military-grade protection.
High-Security Bullet Resistant Doors
What's the Common Materials Used?
Composite Laminates: These doors may also feature layered composite materials, such as Kevlar and fiberglass, to increase the ability to absorb and distribute the energy from bullets.
Ballistic Glass: For areas requiring visibility, ballistic glass or transparent polycarbonate materials are used, providing both security and transparency.
Wha's the Protection Level
Level 5: Withstands .308 Winchester or similar military-grade ammunition.
Wha's the Use Cases
Jewelry Stores or Banks: Environments that deal with high-value assets that could be subject to armed robberies.
Blast-Resistant Bulletproof Doors
What's Protection Level?
Commonly found in government buildings, embassies, military sites, and critical infrastructure where both bullet and blast threats are present.
Fire-Rated Bullet Resistant Doors
What's Protection Level?
Suitable for industrial buildings, data centers, and commercial properties where fire safety and bulletproofing are equally important.
Custom Bullet Resistant Doors
What's Protection Level?
These doors are often used in unique or high-risk environments such as executive offices, high-net-worth residential properties, jewelry stores, and secure vaults.
Transparent Bullet Resistant Doors
What's Protection Level?
These are commonly used in banks, correctional facilities, military installations, and any location where clear visibility without compromising security is necessary.
Sliding Bullet Resistant Doors
What's Protection Level?
Often used in commercial spaces such as banks, casinos, and government buildings where space efficiency is important but security cannot be compromised.
The Apostle Paul had to deal with some problems going on in the Corinthian church. He dealt with some moral concerns and also corrected some doctrinal issues including the resurrection. Because of the resurrection of Christ we have hope. Click on the link below to read the encouraging reason why. #1Corinthians #BibleStudy #Devotions #Hope
Thank you Papi Promotions Community for being able to share this info
Welcome to Junique's Gospel Musical Review, where the rhythm of urban gospel meets unparalleled opportunities for growth and connection!
We are thrilled to offer you an exclusive experience that goes beyond music, providing you with
**free membership**,
**free urban gospel newsletters**, and
**special discounts on ad packages for All Nations TV**.
Our platform also connects you with
**thriving social media communities boasting thousands of members**,
**top-tier urban gospel promotion services**,
and the **prestigious Gospel Industry Network**.
Enjoy additional perks like
**discounts on Junique’s ad services**
https://youtu.be/XV2MbOSb-I4and much more as we empower you to take your ministry, music, or brand to the next level.
Dive in, and let's celebrate gospel excellence together!
The Apostle Paul admitted in Philippians of the errors in his life he lived before he experienced Jesus. He wrote about how much the Lord meant to him. Click on the link below to gain practical wisdom from the apostle. #316 #BibleStudy #Devotions #Discipleship #Philippians
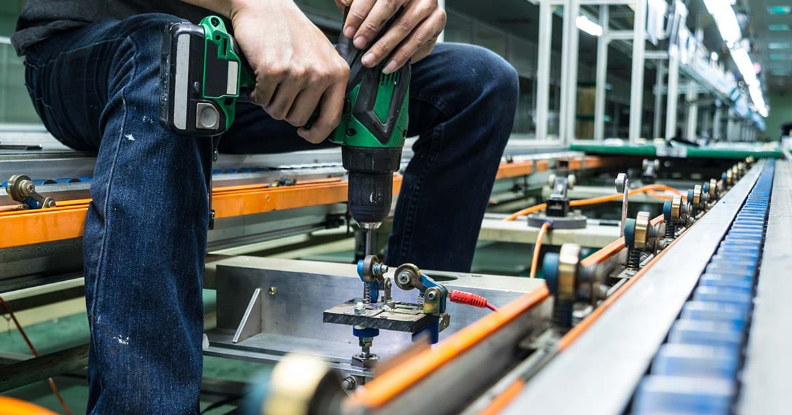
Why Does the Angle Matter in Conveyor Belt Installation?
What Are the Key Factors Influencing Conveyor Belt Angles?
The nature of the items being transported plays a significant role in conveyor belt installation design. Lightweight, smooth items like envelopes might handle steeper angles without slipping, while heavier or bulkier goods—like retail packages—require gentler slopes. The coefficient of friction between the belt surface and the material is a critical metric here. For instance, belts with textured surfaces or cleats can support steeper angles by preventing rollback, a feature often integrated into intelligent sorting systems.
The construction of the conveyor belt itself—whether modular, rubber, or fabric-based—impacts the feasible angle. During conveyor belt installation, tension must be carefully adjusted to maintain grip without overstressing the system. Overly steep angles can increase tension beyond the belt’s capacity, leading to premature wear or mechanical failure. Advanced systems, such as those used in e-commerce sorting, often employ belts with specialized coatings to optimize performance at varying inclines.
In high-speed sorting environments, such as courier express parcel hubs, the conveyor belt angle must align with operational tempo. A steep incline might slow down material flow due to gravity resistance, while a flat or slight incline can maintain momentum. Conveyor belt installation must account for how angle adjustments affect sorting accuracy and delivery timelines, especially in automated setups where sensors and diverters rely on consistent material positioning.
What Is the Industry Standard for Conveyor Belt Angles?
- 0° to 10°: Ideal for fragile or loose items, ensuring minimal disruption. Common in wholesale and retail sorting.
- 10° to 20°: A versatile range for most packaged goods, balancing space efficiency and stability. Widely used in logistics operators.
- 20° to 30°: Suitable for compact systems with high-friction belts or cleats, often seen in e-commerce facilities with space constraints.
- Angles beyond 30° are rare without additional support mechanisms like sidewalls or custom belt designs, as slippage and energy costs rise significantly. During conveyor belt installation, testing the chosen angle under real-world loads is essential to validate performance.
How Does Conveyor Belt Installation Angle Affect Efficiency?
The steeper the angle, the more power a conveyor system requires to lift materials against gravity. In energy-conscious designs—common in modern logistics networks—engineers aim to minimize incline angles while meeting spatial needs. For example, a 15° incline might double the motor power demand compared to a flat belt, impacting long-term operational costs. Conveyor belt installation should thus prioritize angles that align with sustainability goals without sacrificing throughput.
In densely packed facilities, such as urban e-commerce warehouses, vertical space is a premium. A steeper conveyor belt angle can reduce the system’s footprint, allowing more room for sorting equipment or storage. However, this must be weighed against potential trade-offs in material control. Intelligent systems often integrate multi-tiered conveyors with moderate inclines (e.g., 15°–20°) to strike this balance.
Steep angles increase stress on belts, rollers, and motors, accelerating wear. Conveyor belt installation designs that push beyond recommended inclines may require more frequent retrofits or part replacements. In contrast, gentler slopes extend equipment lifespan, a key consideration for systems handling high volumes, like those in courier services.
What Are Best Practices for Conveyor Belt Installation Angles?
Before finalizing the angle, simulate material flow under various inclines. This step ensures the conveyor belt installation supports the specific goods—whether lightweight parcels or heavy wholesale items—without slippage or jams. Advanced sorting systems often use test runs to calibrate angles for peak efficiency.
For angles above 15°, consider adding cleats, side guards, or textured surfaces to the belt. These enhancements, common in intelligent conveying solutions, stabilize materials and expand the range of viable inclines. During conveyor belt installation, these features should be tailored to the system’s purpose, such as high-speed parcel sorting.
In smart sorting systems, sensors can monitor material behavior in real time, adjusting belt speed or angle dynamically (if the system allows). This adaptability reduces the risks of steep inclines, ensuring consistent performance. Conveyor belt installation in such setups often integrates these technologies for precision and reliability.
How Do Real-World Applications Shape Conveyor Belt Angles?
Conclusion: Finding the Sweet Spot for Conveyor Belt Installation
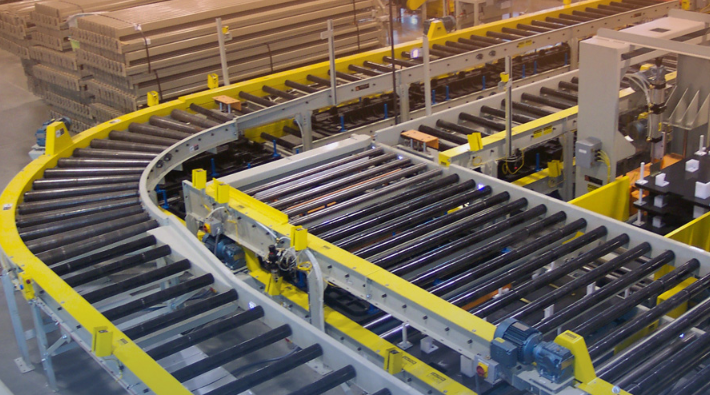
The Mechanics Behind Live Roller Conveyors
Why Are Live Roller Conveyors Essential for Intelligent Sorting?
Integration with Smart Infrastructure
A live roller conveyor doesn’t operate in isolation—it’s part of a broader digital logistics network. Sensors and control systems can be embedded along the conveyor to monitor item flow, detect jams, or redirect packages based on real-time data. This integration aligns with the “efficiency-based” mission seen in advanced sorting solutions, enabling operators to optimize throughput and reduce downtime.
Handling Diverse Loads
How Do Live Roller Conveyors Compare to Other Conveyor Systems?
Advantages of Live Roller Conveyors
Limitations to Consider
What Innovations Are Shaping the Future of Live Roller Conveyors?
Smart Technology Integration
Energy Efficiency and Sustainability
Customization for Emerging Markets
Conclusion
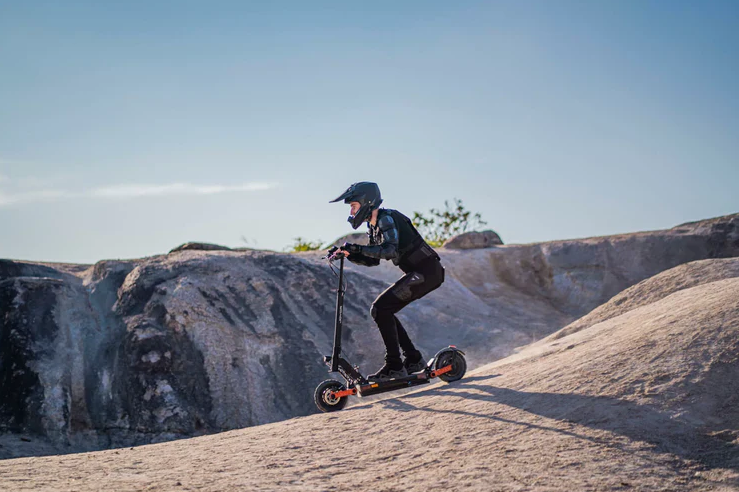
What Makes an Off-Road Electric Scooter Different?
- Motor Power: Off-road electric scooters typically feature high-wattage motors (often 1000W or more) to provide the torque needed for steep inclines and uneven surfaces. Dual-motor models are also common, offering enhanced traction on slippery or rocky paths.
- Tire Design: Pneumatic, knobby tires with deep treads are standard for off-road electric scooters. These tires provide better grip on dirt, gravel, and mud compared to the smaller, solid tires found on city scooters.
- Suspension Systems: To absorb shocks from rough terrain, off-road electric scooters are equipped with advanced suspension systems, such as dual hydraulic or spring suspensions. This ensures a smoother ride over bumps and dips.
- Frame Durability: The frame of an off-road electric scooter is often made from reinforced aluminum alloy or steel to withstand the stress of off-road conditions.
What Terrains Can an Off-Road Electric Scooter Handle?
Dirt trails are a common testing ground for off-road electric scooters. With the right tire tread and motor power, these scooters can glide over loose soil and small rocks. The suspension system plays a crucial role here, preventing the rider from feeling every jolt. For example, a 1200W off-road electric scooter with 10-inch pneumatic tires can maintain stability on uneven forest paths, provided the rider maintains balance.
Gravel roads and rocky terrains pose a greater challenge due to their unevenness and lack of traction. An off-road electric scooter with wider tires and a higher ground clearance (typically 6 inches or more) can manage these conditions better. The key is to avoid sudden acceleration, which can cause the tires to lose grip on loose stones.
Mud and water introduce additional complexity. While many off-road electric scooters are water-resistant (with IP ratings like IP54 or higher), prolonged exposure to deep mud can damage components like the motor or battery if not properly sealed. Riders should look for scooters with sealed electronics and avoid submerging the scooter in water. Slow, steady movements are essential to maintain control in slippery conditions.
Climbing steep hills requires significant torque, which is why off-road electric scooters often boast powerful motors. A scooter with a 1500W motor and a climbing angle of 20 degrees or more can tackle most inclines. However, battery drainage accelerates on steep terrain, so riders should ensure their scooter has a high-capacity battery (e.g., 48V or higher) for longer trips.
Key Features to Look for in an Off-Road Electric Scooter
Off-road riding consumes more power than urban commuting due to increased resistance and incline challenges. A high-quality off-road electric scooter should have a battery range of at least 30-50 miles per charge, depending on terrain and rider weight. Lithium-ion batteries with capacities of 15Ah or higher are ideal for extended off-road adventures.
Safety is paramount when riding off-road. An off-road electric scooter should be equipped with reliable braking systems, such as hydraulic disc brakes or regenerative braking, to ensure quick stops on unpredictable terrain. Dual braking systems (front and rear) provide added control, especially on steep descents.
While off-road electric scooters are generally heavier due to their robust build (often weighing 50-80 lbs), portability remains a consideration for those who need to transport them. Some models feature foldable designs, making them easier to carry or store when not in use.
Speed is less of a priority off-road compared to stability, but a good off-road electric scooter should still offer adjustable speed settings. Most models can reach speeds of 20-40 mph on flat surfaces, though riders should reduce speed on rough terrain to maintain control.
Safety Tips for Riding an Off-Road Electric Scooter
- Wear Protective Gear: Always wear a helmet, knee pads, elbow pads, and gloves. Off-road conditions increase the likelihood of falls, and proper gear can prevent serious injuries.
- Inspect Your Scooter: Before heading out, check the tire pressure, brakes, and battery charge. Ensure all components are functioning properly to avoid breakdowns in remote areas.
- Ride Within Limits: Avoid pushing the scooter beyond its capabilities. For example, don’t attempt steep inclines if the scooter’s motor isn’t powerful enough, as this can lead to overheating or stalling.
- Stay Visible: If riding in low-light conditions, equip your off-road electric scooter with LED lights and wear reflective clothing to enhance visibility.
Environmental Benefits of Choosing an Off-Road Electric Scooter
Maintenance Tips for Longevity of an Off-Road Electric Scooter
- Clean After Every Ride: Remove dirt, mud, and debris from the tires, frame, and undercarriage to prevent corrosion or damage to moving parts. Use a damp cloth and avoid high-pressure water jets near electrical components.
- Check Tire Condition: Off-road riding can wear out tires quickly. Inspect for punctures or excessive wear and replace them as needed to maintain traction.
- Battery Care: Store the scooter in a cool, dry place and avoid fully draining the battery. Charge it after every ride to prolong battery life.
- Lubricate Moving Parts: Apply lubricant to the suspension and folding mechanisms (if applicable) to keep them functioning smoothly after exposure to dust or mud.
Final Thoughts on Off-Road Electric Scooters
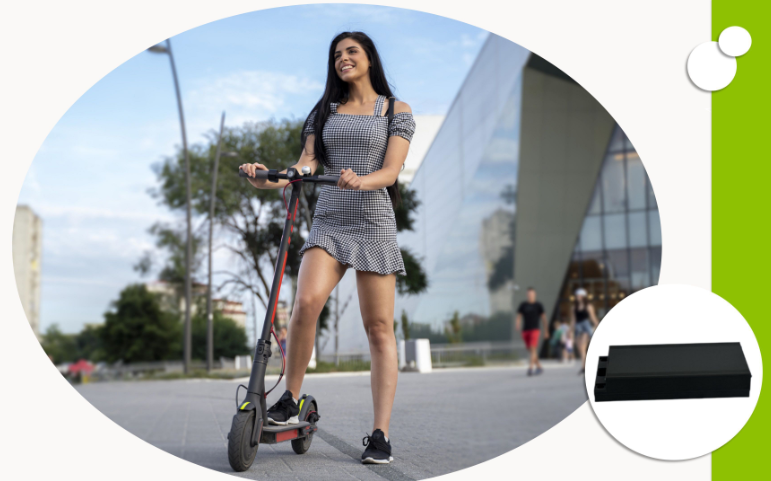
The Basics of an Electric Scooter Lithium Battery
What Factors Affect the Lifespan of an Electric Scooter Lithium Battery?
Temperature is another critical factor. Electric scooter lithium batteries thrive in moderate conditions, typically between 20°C and 25°C (68°F to 77°F). Exposure to extreme heat—like leaving a scooter in direct sunlight—can degrade the battery’s electrolyte, while cold temperatures can reduce its efficiency and capacity. For users in regions with harsh climates, proper storage becomes vital to preserving battery health.
The way an electric scooter is used also affects the battery’s longevity. High-speed riding, frequent acceleration, or carrying heavy loads increases the power demand on the electric scooter lithium battery, leading to faster depletion of charge cycles. Scooters designed for casual urban commuting, such as those produced by Zhejiang Dece Power Co., Ltd., are optimized for efficiency, but aggressive usage can still shorten battery life.
Not all electric scooter lithium batteries are created equal. Batteries manufactured with high-grade materials and stringent quality controls—like those adhering to ISO9001 or CE certifications—tend to outlast cheaper alternatives. Companies prioritizing innovation and quality in their production processes ensure that their batteries meet international standards, offering users a more reliable product.
How Long Does an Electric Scooter Lithium Battery Typically Last?
- Charge Cycles: A battery rated for 500 cycles, used once daily, could last roughly 1.5 years. If charged every other day, it might extend to 3 years.
- Mileage: For scooters with a range of 20-30 kilometers per charge, a 500-cycle battery could provide 10,000 to 15,000 kilometers of total travel.
- Real-World Use: Daily commuters might see a shorter lifespan (2-3 years), while occasional users could stretch it to 5 years or more.
How Can You Extend the Life of an Electric Scooter Lithium Battery?
Avoid charging the battery to 100% or letting it drop to 0% regularly. Instead, aim for partial charges within the 20%-80% range. Using a charger compatible with your scooter’s specifications—such as those provided by reputable manufacturers—also prevents overvoltage damage.
When not in use, store your electric scooter lithium battery in a cool, dry place away from direct sunlight or freezing temperatures. For long-term storage (e.g., over winter), keep the battery at around 50%-60% charge to minimize capacity loss.
Smooth acceleration, moderate speeds, and avoiding excessive weight can reduce strain on the battery. For scooters designed for versatility—like those from Zhejiang Dece Power Co., Ltd.—following recommended usage guidelines ensures the electric scooter lithium battery performs optimally over time.
Periodically check the battery for signs of wear, such as reduced range or slower charging times. If your scooter supports it, use diagnostic tools or apps to monitor battery health. Addressing issues early can prevent further degradation.
What Happens When an Electric Scooter Lithium Battery Reaches the End of Its Life?
Conclusion: Making the Most of Your Electric Scooter Lithium Battery
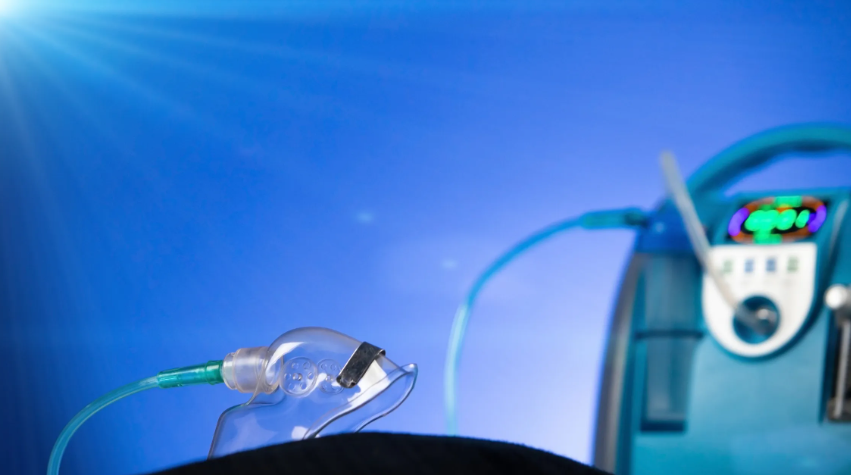
What Is Boost Oxygen, and Why Does It Matter for Air Travel?
Can I Take Boost Oxygen on a Plane? TSA and Airline Regulations
How Does Boost Oxygen Differ from Medical Oxygen on Flights?
Why Can’t I Take Boost Oxygen on a Plane? Safety and Science Explained
Alternatives to Boost Oxygen for Air Travelers
The Role of Air Separation Technology in Portable Oxygen Solutions
Final Thoughts: Can I Take Boost Oxygen on a Plane?
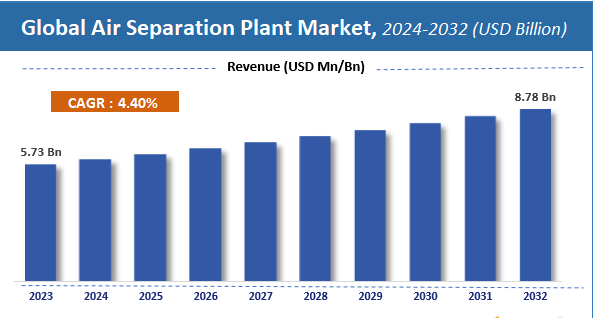
Understanding the Air Separation Unit Market Size
Key Drivers of the Air Separation Unit Market Growth
How Do Technologies Shape the Air Separation Unit Market?
Cryogenic distillation remains the backbone of the air separation unit market, especially for high-volume, high-purity gas production. This process cools air to extremely low temperatures, separating it into liquid oxygen, nitrogen, and argon via fractional distillation. It’s ideal for large-scale applications, such as steel mills or chemical plants, and aligns with products like Z-Oxygen’s cryogenic air separation series deployed in Russia. The air separation unit market benefits from cryogenic systems’ ability to co-produce liquid gases, meeting demands for low-temperature storage solutions.
Non-cryogenic technologies, particularly PSA, are carving a growing niche in the air separation unit market. PSA systems use adsorbent materials to selectively capture gases, offering a cost-effective, energy-efficient alternative for smaller-scale oxygen or nitrogen generation. This technology suits applications like Z-Oxygen’s PSA nitrogen generators in Thailand or container oxygen generators in Chile, where portability and simplicity are key. The air separation unit market sees PSA’s rise due to its flexibility and lower operational costs, appealing to industries with moderate gas needs.
Advancements in membrane separation and intelligent control valves—areas where Z-Oxygen also excels—are further shaping the air separation unit market. These innovations enhance efficiency, reduce energy consumption, and enable customization of gas purity levels, aligning with sustainability goals and
Where Is the Air Separation Unit Market Growing Fastest?
Asia-Pacific dominates the air separation unit market, accounting for the largest share and the fastest growth. Rapid industrialization in China, India, and Southeast Asia fuels demand for industrial gases, supported by steel production, electronics manufacturing, and healthcare investments. China alone produces over half of the world’s steel, relying heavily on ASUs. Projects like Z-Oxygen’s PSA nitrogen generators in Thailand exemplify this region’s appetite for air separation solutions, making it a hotspot for market expansion.
In North America and Europe, the air separation unit market emphasizes technological upgrades and sustainability. The U.S., a net exporter of crude oil, uses ASUs for enhanced oil recovery, while Europe invests in energy-efficient systems to meet strict environmental regulations. These regions prioritize advanced ASUs, such as those with digital controls or carbon capture integration, reflecting a mature but evolving market.
Countries like Turkey, South Africa, and Chile—where Z-Oxygen has deployed liquid oxygen storage tanks, oil-free compressors, and container oxygen generators—represent emerging opportunities in the air separation unit market. Industrial growth and healthcare needs in these regions drive demand for both large-scale and modular ASU solutions.
What Challenges and Opportunities Lie Ahead for the Air Separation Unit Market?
High initial investment costs and energy-intensive operations pose challenges for the air separation unit market. Cryogenic systems, while efficient for large-scale production, require significant capital and power, potentially limiting adoption in cost-sensitive regions. PSA systems mitigate this but may not scale as effectively for massive industrial needs.
On the flip side, the air separation unit market is ripe with opportunities. The shift toward energy-efficient ASUs, renewable energy integration, and tailored gas purity solutions aligns with global sustainability goals. Companies innovating in these areas—like Z-Oxygen with its intelligent control valves—can tap into growing demand across diverse industries.
Looking ahead to 2030 and beyond, the air separation unit market is poised for robust growth. Analysts predict a market size approaching USD 10 billion by 2034, driven by industrialization, healthcare advancements, and clean energy initiatives. The versatility of ASU technologies ensures their relevance, whether for large cryogenic plants or portable PSA units.
Conclusion
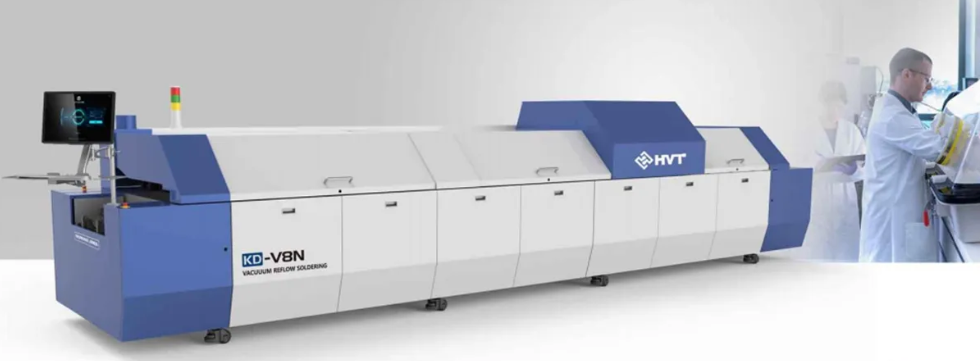
Preventing Oxidation During the Reflow Process
Enhancing Solder Joint Quality and Reducing Voids
Improving Wetting Performance for Complex Assemblies
How Does a Nitrogen Reflow Oven Impact Production Efficiency?
Defective solder joints are a common cause of rework in electronics manufacturing, adding time and cost to the production process. Issues like incomplete wetting, excessive voiding, or oxidation-related failures often necessitate manual inspection and repair. By using a nitrogen reflow oven, manufacturers can significantly reduce these defects, leading to a higher first-pass yield—the percentage of products that meet quality standards without requiring rework.
The electronics industry is constantly evolving, with new materials and soldering techniques emerging to meet the demands of next-generation devices. For example, the rise of lead-free solders and the increasing complexity of power devices like IGBT modules require soldering processes that can handle higher temperatures and more challenging conditions. A nitrogen reflow oven is well-suited to these advanced applications, as it provides the controlled atmosphere needed to work with sensitive materials without compromising quality.
What Are the Challenges of Using a Nitrogen Reflow Oven?
Process Optimization and Training Requirements
Conclusion: The Future of Nitrogen Reflow Ovens in Electronics Manufacturing
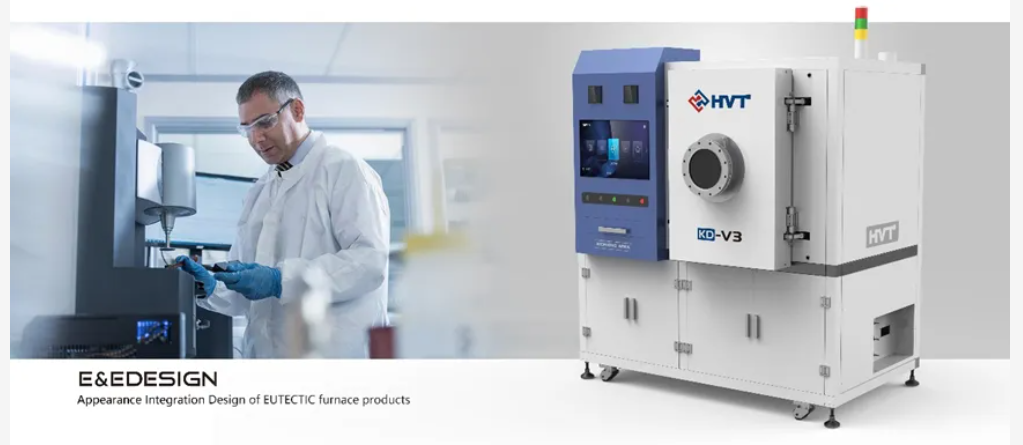
The Role of Vacuum Ovens in Semiconductor Production
Key Benefits of Using a Vacuum Oven in Semiconductor Processes
Moisture trapped within semiconductor components can lead to voids during welding or encapsulation, compromising structural integrity. A vacuum oven mitigates this by lowering the boiling point of water, enabling drying at temperatures as low as 40-60°C. For example, a vacuum oven for sale with advanced pressure control can reduce drying times to 30-60 minutes for thin films, a common need in power device packaging—an area where Chengliankaida collaborates with the IGBT industry alliance.
Hermetic packaging is essential for protecting semiconductors from environmental factors like humidity or oxidation. A vacuum oven prepares components by removing residual gases and moisture, ensuring a tight seal during encapsulation. This aligns with the expertise of companies like Chengliankaida, which has earned praise for solving hermeticity challenges, making a vacuum oven for sale a critical investment for similar manufacturers aiming for flawless seals.
Semiconductor production involves diverse materials, from silicon wafers to metal casings. A vacuum oven’s ability to handle varying thicknesses and compositions makes it indispensable. When evaluating a vacuum oven for sale, look for adjustable settings to accommodate both delicate coatings and robust assemblies, reflecting the adaptability seen in Chengliankaida’s production lines.
How Vacuum Ovens Enhance Power Device Manufacturing
Technical Features to Look for in a Vacuum Oven
- Vacuum Pump Quality: A strong pump achieving pressures below 1 mbar ensures rapid moisture removal.
- Temperature Uniformity: Even heat distribution prevents hotspots that could damage delicate components.
- Chamber Design: Stainless steel interiors resist corrosion, while shelf configurations optimize batch processing.
- Control Systems: Digital interfaces allow precise adjustments, a must for repeatable results.
Real-World Applications and Drying Times
- Thin Adhesive Layers: Used in chip bonding, these might dry in 30-60 minutes at 50°C under vacuum.
- Substrate Preparation: Silicon wafers or ceramic bases may take 2-4 hours, depending on thickness and moisture levels.
- Degassing Epoxies: For encapsulation, a vacuum oven can complete the process in 1-3 hours, ensuring bubble-free results.
Challenges and Solutions in Vacuum Oven Use
The Future of Vacuum Ovens in High-Tech Industries
Conclusion: A Critical Tool for Precision Manufacturing
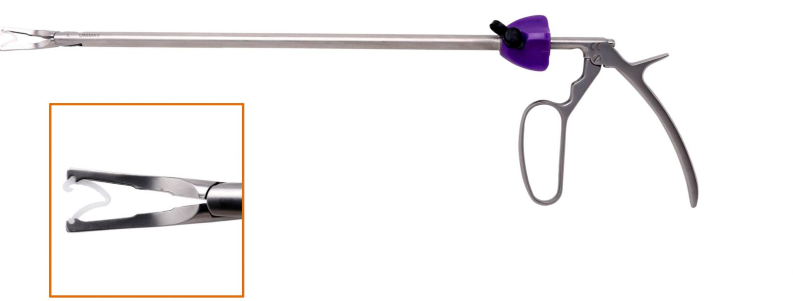
Understanding the Role of the Endoclip Applier in Surgery
The success of the endoclip applier lies in its ability to provide a non-suturing method for achieving hemostasis and tissue closure, which is particularly valuable in delicate procedures. For instance, in laparoscopic cholecystectomy (gallbladder removal), the endoclip applier is often used to clip the cystic duct and artery, preventing bile leakage or bleeding. Similarly, in endoscopic procedures like polypectomies, it helps manage post-resection bleeding by sealing vessels effectively.
Factors Influencing the Success Rate of Endoclip Appliers
· Surgeon Experience and Technique: The precision with which the endoclip applier is used significantly impacts its efficacy. Experienced surgeons who are well-versed in laparoscopic techniques tend to achieve higher success rates due to their ability to position clips accurately, even in challenging anatomical locations.
· Device Design and Quality: Not all endoclip appliers are created equal. High-quality devices, such as those produced by companies specializing in minimally invasive surgical instruments, offer features like 360-degree rotation, ergonomic handles, and reliable clip deployment mechanisms. These design elements reduce the risk of misfiring or clip slippage, thereby enhancing success rates.
· Patient-Specific Factors: The condition of the tissue being clipped plays a role in outcomes. For example, inflamed or fibrotic tissues may not hold clips as securely as healthy tissues, potentially leading to clip migration or failure. Patient comorbidities, such as coagulopathies, can also affect the success of hemostasis achieved with the endoclip applier.
· Type of Procedure: The success rate varies across procedures. In gastrointestinal endoscopy, endoclips are highly effective for controlling bleeding, with success rates often exceeding 90%. In contrast, more complex applications, such as managing large perforations, may have slightly lower success rates due to the technical challenges involved.
Clinical Applications and Success Rates Across Specialties
· General Surgery: In procedures like laparoscopic appendectomy or cholecystectomy, the endoclip applier is commonly used to secure vessels or ducts. Studies indicate a success rate of approximately 95% in preventing postoperative bleeding or bile leaks when clips are applied correctly. Failures are rare and often attributed to improper clip sizing or tissue characteristics.
· Urology and Gynecology: In laparoscopic urologic or gynecologic surgeries, the endoclip applier is used to control bleeding or secure structures like the ureter or ovarian vessels. Success rates in these fields are generally high, often exceeding 90%, thanks to the precision offered by modern laparoscopic systems and the reliability of the clips themselves.
· Thoracic Surgery: In minimally invasive thoracic procedures, such as video-assisted thoracoscopic surgery (VATS), the endoclip applier assists in managing vascular structures or sealing air leaks. While data specific to thoracic applications is less abundant, success rates are estimated to be around 85% to 90%, with challenges arising from the confined working space and the need for meticulous clip placement.
Challenges and Limitations of Endoclip Appliers
· Clip Migration or Dislodgement: In rare cases, clips may dislodge from the target tissue, leading to complications like bleeding or leakage. This issue, though uncommon, underscores the importance of selecting appropriately sized clips and ensuring secure application with the endoclip applier.
· Technical Difficulties in Complex Cases: In scenarios involving large defects or highly inflamed tissues, the endoclip applier may struggle to achieve adequate closure. For instance, closing large gastrointestinal perforations may require multiple clips or alternative techniques, reducing the overall success rate to around 80% in such cases.
· Learning Curve: While the endoclip applier is relatively straightforward to use, less experienced surgeons may encounter difficulties in achieving optimal clip placement, especially in anatomically challenging areas. Training and simulation can help mitigate this limitation, improving success rates over time.
Advances in Endoclip Applier Technology
· Enhanced Clip Designs: Modern endoclips are designed with improved gripping mechanisms, reducing the risk of slippage. Some clips are also MRI-compatible, allowing for safe postoperative imaging without interference.
· Ergonomic Appliers: Newer endoclip applier models feature ergonomic designs that enhance surgeon comfort and precision. Features like adjustable firing mechanisms and visual feedback systems help ensure accurate clip deployment.
· Integration with Endoscopic Systems: Advances in endoscopic visualization have complemented the use of the endoclip applier, providing surgeons with clearer images and better control during procedures. This synergy has contributed to higher success rates, particularly in gastrointestinal applications.
Conclusion: The Future of Endoclip Appliers in Minimally Invasive Surgery
As technology continues to advance, we can expect further improvements in the design and functionality of the endoclip applier, potentially pushing success rates even higher. For now, its role in enhancing patient outcomes through minimally invasive techniques is undeniable, providing a balance of efficacy and safety that benefits both surgeons and patients alike. By understanding its applications, limitations, and potential, medical professionals can continue to refine their techniques and contribute to the ongoing evolution of surgical care.
This article provides a detailed, professional guide on sterilizing reusable laparoscopic trocars, drawing on best practices and technical expertise without promoting specific products.
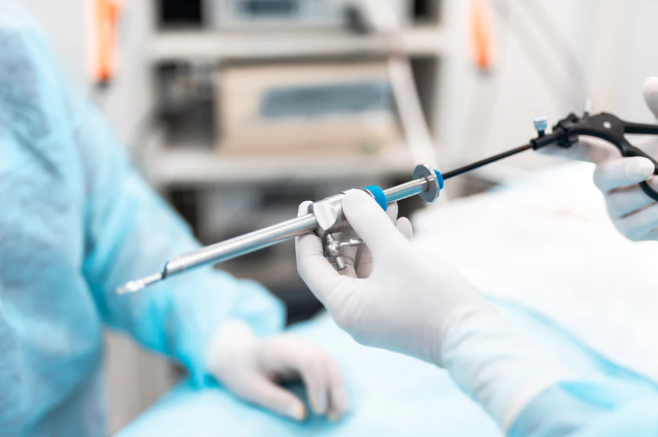
What Are Reusable Laparoscopic Trocars and Why Sterilization Matters?
The importance of sterilization cannot be overstated. Inadequate processing can compromise patient outcomes, especially in sensitive fields like gynecology or thoracic surgery, where precision and hygiene are paramount. Compliance with international standards, such as ISO 13485 for medical device quality management and CE marking for safety, underscores the need for rigorous sterilization practices.
How Should Reusable Laparoscopic Trocars Be Cleaned Before Sterilization?
Step 1: Immediate Post-Use Rinsing
After surgery, rinse reusable laparoscopic trocars under cold running water to remove gross contaminants. Cold water prevents proteins from coagulating, which could complicate later cleaning. Avoid soaking at this stage to prevent corrosion of metal components.
Step 2: Disassembly
Most reusable laparoscopic trocars consist of detachable parts—cannulas, obturators, and seals. Disassemble them according to the manufacturer’s instructions. This ensures all surfaces, including hard-to-reach areas like valve mechanisms, are accessible for cleaning.
Step 3: Manual or Ultrasonic Cleaning
Use a neutral-pH enzymatic detergent designed for medical instruments. Manual cleaning involves brushing internal channels and external surfaces with soft, non-abrasive tools to avoid damaging delicate components. Alternatively, ultrasonic cleaning can dislodge debris from intricate areas of reusable laparoscopic trocars. Ensure the cleaning solution reaches all parts, followed by a thorough rinse with distilled water to remove detergent residue.
Step 4: Drying
Dry the trocars with lint-free cloths or compressed air. Residual moisture can interfere with sterilization and promote microbial growth, especially in the narrow lumens of reusable laparoscopic trocars.
What Disinfection Methods Prepare Reusable Laparoscopic Trocars for Sterilization?
Chemical Disinfection
Soaking disassembled trocars in a high-level disinfectant, such as glutaraldehyde or ortho-phthalaldehyde (OPA), targets resistant pathogens. Exposure times vary (typically 10-20 minutes), and strict adherence to concentration and contact time is critical. Rinse thoroughly afterward with sterile water to remove chemical residues, which could harm patients or damage the trocars.
Thermal Disinfection
Some facilities use thermal washers with hot water (e.g., 70-90°C) for disinfection. This method suits reusable laparoscopic trocars made of heat-resistant materials like stainless steel, common in MIS instruments. However, check compatibility, as seals or plastic components may degrade under high temperatures.
Disinfection is a bridge to sterilization, not a substitute. It prepares reusable laparoscopic trocars for the final, definitive elimination of all microorganisms.
How Are Reusable Laparoscopic Trocars Sterilized for Surgical Use?
Steam Autoclaving (Moist Heat Sterilization)
Steam sterilization in an autoclave is the most common method for reusable laparoscopic trocars made of stainless steel or other heat-tolerant materials. Typical parameters are 121°C for 15-20 minutes or 134°C for 3-5 minutes at 15-30 psi. Pre-vacuum cycles remove air from lumens, ensuring steam penetrates all areas. After sterilization, allow the trocars to cool and dry to prevent moisture-related contamination.
Low-Temperature Sterilization
For trocars with heat-sensitive components (e.g., rubber seals), low-temperature methods like ethylene oxide (ETO) or hydrogen peroxide gas plasma are ideal. ETO sterilization requires aeration to remove toxic residues, taking 12-24 hours total, while hydrogen peroxide plasma is faster (45-60 minutes) and residue-free. Both methods suit the complex designs of reusable laparoscopic trocars used in specialties like urology or gynecology.
Validation and Monitoring
Sterilization isn’t complete without verification. Use biological indicators (e.g., Bacillus spores) to confirm the process’s efficacy, alongside chemical indicators to ensure proper exposure. Regular maintenance of sterilization equipment is equally vital to guarantee consistent results for reusable laparoscopic trocars.
What Are the Challenges in Sterilizing Reusable Laparoscopic Trocars?
Complex Geometry
Narrow lumens, valves, and articulated components can trap debris or sterilants, necessitating meticulous cleaning and advanced sterilization cycles. Incomplete processing risks contamination, particularly in thoracic or general surgery applications.
Material Compatibility
Reusable laparoscopic trocars often combine metals, plastics, and elastomers. High heat may warp plastics, while certain chemicals can corrode metals. Selecting the right sterilization method is critical to preserve functionality.
Human Error
Inconsistent adherence to protocols—skipping disassembly, inadequate rinsing, or improper drying—can compromise sterility. Training staff and standardizing procedures mitigate these risks.
How Can You Ensure Reusable Laparoscopic Trocars Remain Safe Over Time?
Regular Inspection
Before and after sterilization, inspect trocars for wear, corrosion, or damage. Cracked seals or dull tips can harbor microbes or fail during surgery. Replace faulty parts promptly.
Proper Storage
Store sterilized reusable laparoscopic trocars in a clean, dry, dust-free environment, ideally in protective trays or pouches. This prevents recontamination before use in procedures like obstetrics or urology.
Reprocessing Limits
Unlike disposable trocars, reusable laparoscopic trocars have a finite lifespan. Follow manufacturer guidelines on maximum reprocessing cycles to ensure safety and performance aren’t compromised.