To expand your news reach, consider advertising with our media partner, Patch Media, at https://heypapipromotionsmedia.town.news/. Patch is a nationwide news network comprising over 1,000 hyperlocal websites dedicated to community news across the United States. For press release distribution services, please call or visit https://heypapipromotions.com/advertise.
The electronics manufacturing industry relies heavily on precision and reliability, especially when producing semiconductor devices and power electronics. A nitrogen reflow oven is a specialized piece of equipment designed to optimize the soldering process during surface-mount assembly. But why exactly is nitrogen introduced into the reflow oven environment? This section delves into the primary reasons and technical benefits of using nitrogen in such systems.
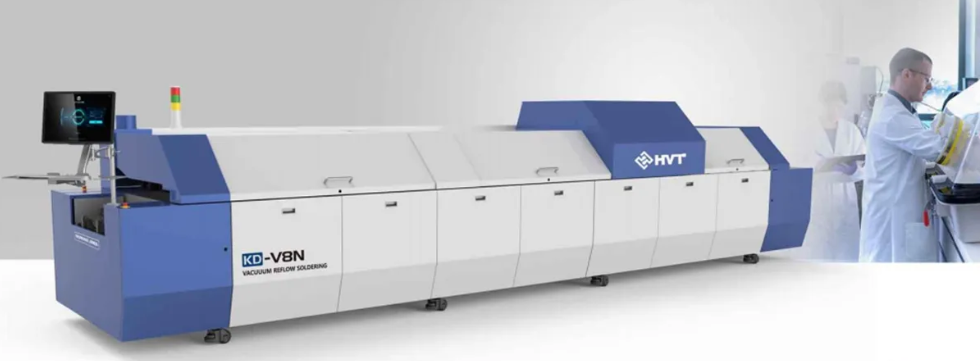
Preventing Oxidation During the Reflow Process
One of the most significant advantages of using a nitrogen reflow oven is its ability to minimize oxidation. During the reflow soldering process, electronic components are exposed to high temperatures to melt solder paste and form reliable joints. In an oxygen-rich environment, both the solder and the metallic surfaces of components can oxidize. Oxidation creates a thin layer of oxide that hinders proper wetting of the solder, leading to weak joints and potential failures in the final product.
By introducing nitrogen into the reflow oven, the oxygen content in the atmosphere is drastically reduced. Nitrogen, as an inert gas, does not react with metals or solder alloys at the temperatures used in reflow soldering (typically between 200°C and 300°C). This creates a protective environment that prevents oxide formation, ensuring cleaner and more reliable solder joints. For manufacturers working on high-precision semiconductor devices, such as those produced by companies like Chengliankaida Technology Co., LTD, this is critical for achieving the hermetic sealing and low void rates demanded by modern applications.
Enhancing Solder Joint Quality and Reducing Voids
Another key reason for using a nitrogen reflow oven is its impact on solder joint quality. Solder joints are the backbone of electronic assemblies, and their integrity directly affects the performance and longevity of the final product. In an air-based reflow process, trapped oxygen can lead to the formation of voids—small gas pockets within the solder joint. These voids can weaken the mechanical strength of the joint and impair its thermal and electrical conductivity, which is particularly problematic for power devices and high-frequency semiconductor components.
A nitrogen reflow oven mitigates this issue by displacing oxygen and creating a more stable soldering environment. The inert atmosphere reduces the likelihood of gas entrapment during the solder’s liquid phase, leading to fewer voids. Research has shown that nitrogen reflow soldering can reduce void rates by up to 50% compared to air-based systems, depending on the process parameters and solder paste composition. For industries focused on high-reliability applications—like IGBT modules or advanced semiconductor packaging—this improvement is invaluable.
Improving Wetting Performance for Complex Assemblies
Wetting refers to the ability of molten solder to spread and adhere to the surfaces of components and circuit boards. Poor wetting can result in incomplete solder joints, leading to electrical discontinuities or mechanical failures over time. In a standard air atmosphere, oxidation on component leads or PCB pads can impede wetting, especially for complex assemblies with fine-pitch components or lead-free solders, which are more prone to oxidation due to their higher tin content.
A nitrogen reflow oven enhances wetting performance by maintaining a clean, oxide-free surface during the soldering process. This is particularly beneficial for lead-free soldering, which has become the industry standard due to environmental regulations like RoHS (Restriction of Hazardous Substances). Lead-free solders often require higher reflow temperatures and are more sensitive to oxidation, making the use of nitrogen even more critical. For manufacturers specializing in semiconductor device packaging, such as those developing advanced power devices, this
ensures consistent quality across production batches.
How Does a Nitrogen Reflow Oven Impact Production Efficiency?
While the technical benefits of using nitrogen in a reflow oven are clear, its impact on overall production efficiency is equally important. Let’s explore how this technology influences manufacturing workflows, defect rates, and process optimization.
Reducing Rework and Improving First-Pass Yield
Defective solder joints are a common cause of rework in electronics manufacturing, adding time and cost to the production process. Issues like incomplete wetting, excessive voiding, or oxidation-related failures often necessitate manual inspection and repair. By using a nitrogen reflow oven, manufacturers can significantly reduce these defects, leading to a higher first-pass yield—the percentage of products that meet quality standards without requiring rework.
Defective solder joints are a common cause of rework in electronics manufacturing, adding time and cost to the production process. Issues like incomplete wetting, excessive voiding, or oxidation-related failures often necessitate manual inspection and repair. By using a nitrogen reflow oven, manufacturers can significantly reduce these defects, leading to a higher first-pass yield—the percentage of products that meet quality standards without requiring rework.
For companies involved in the production of semiconductor devices, where precision and reliability are non-negotiable, this improvement in yield translates to substantial cost savings and faster time-to-market. A nitrogen reflow oven ensures that solder joints meet stringent quality standards, minimizing the need for costly rework and enhancing overall production efficiency.
Compatibility with Advanced Materials and Processes
The electronics industry is constantly evolving, with new materials and soldering techniques emerging to meet the demands of next-generation devices. For example, the rise of lead-free solders and the increasing complexity of power devices like IGBT modules require soldering processes that can handle higher temperatures and more challenging conditions. A nitrogen reflow oven is well-suited to these advanced applications, as it provides the controlled atmosphere needed to work with sensitive materials without compromising quality.
The electronics industry is constantly evolving, with new materials and soldering techniques emerging to meet the demands of next-generation devices. For example, the rise of lead-free solders and the increasing complexity of power devices like IGBT modules require soldering processes that can handle higher temperatures and more challenging conditions. A nitrogen reflow oven is well-suited to these advanced applications, as it provides the controlled atmosphere needed to work with sensitive materials without compromising quality.
Moreover, nitrogen reflow ovens are compatible with vacuum-assisted soldering processes, which are often used to achieve ultra-low void rates in high-reliability applications. Companies like those collaborating with universities and industry alliances to develop cutting-edge packaging solutions can leverage this synergy to push the boundaries of what’s possible in semiconductor manufacturing.
What Are the Challenges of Using a Nitrogen Reflow Oven?
While the benefits of a nitrogen reflow oven are undeniable, there are also challenges associated with its implementation. Understanding these challenges can help manufacturers make informed decisions about integrating this technology into their production lines.
Cost and Operational Considerations
One of the primary challenges of using a nitrogen reflow oven is the cost. Nitrogen gas, while relatively inexpensive compared to other inert gases like argon, still adds to the operational expenses of the reflow process. Additionally, maintaining a consistent nitrogen atmosphere requires specialized equipment, such as nitrogen generators or storage systems, as well as monitoring tools to ensure oxygen levels remain below the desired threshold (typically less than 100 ppm for optimal results).
For smaller manufacturers or those with tight budgets, these costs can be a barrier to adoption. However, the long-term benefits—such as reduced defect rates and improved product reliability—often outweigh the initial investment, especially for high-tech enterprises focused on semiconductor packaging and power devices.
Process Optimization and Training Requirements
Implementing a nitrogen reflow oven also requires adjustments to the soldering process. Parameters like nitrogen flow rate, oven temperature profile, and conveyor speed must be carefully optimized to achieve the desired results. This can involve a learning curve for operators and engineers, as well as additional training to ensure consistent performance across production runs.
Despite these challenges, the adoption of nitrogen reflow ovens has become increasingly common in industries where quality and reliability are paramount. For manufacturers committed to innovation and excellence, such as those in the semiconductor and power electronics sectors, these hurdles are a small price to pay for the significant improvements in product performance.
Conclusion: The Future of Nitrogen Reflow Ovens in Electronics Manufacturing
The use of nitrogen in a reflow oven offers a range of technical and operational benefits, from preventing oxidation and improving solder joint quality to enhancing production efficiency and enabling the use of advanced materials. As the electronics industry continues to push the boundaries of performance and reliability, nitrogen reflow ovens will remain a critical tool for manufacturers aiming to meet the stringent demands of modern applications.
For companies involved in the research and development of semiconductor devices and power electronics, such as those partnering with academic institutions and industry alliances, the adoption of nitrogen reflow technology represents a commitment to quality and innovation. While challenges like cost and process optimization exist, the long-term advantages make this technology a worthwhile investment for the future of electronics manufacturing.
Comments