To expand your news reach, consider advertising with our media partner, Patch Media, at https://heypapipromotionsmedia.town.news/. Patch is a nationwide news network comprising over 1,000 hyperlocal websites dedicated to community news across the United States. For press release distribution services, please call or visit https://heypapipromotions.com/advertise.
Conveyor belts are the backbone of modern material handling systems, especially in industries like logistics, e-commerce, and courier services. When it comes to conveyor belt installation, one of the most critical factors to consider is the angle of incline or decline. The angle directly influences throughput, energy efficiency, and system longevity. This article delves into the science and engineering behind determining the best angle for conveyor belt installation, with a focus on applications in intelligent sorting systems.
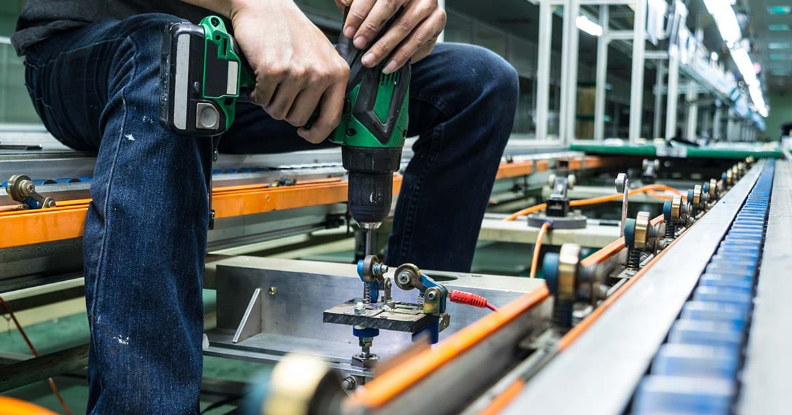
Why Does the Angle Matter in Conveyor Belt Installation?
The angle of a conveyor belt—whether it’s flat, inclined, or declined—affects how materials move, how much power the system consumes, and how stable the operation remains. In intelligent sorting systems, where precision and speed are paramount, an improperly angled conveyor can lead to material slippage, bottlenecks, or excessive wear on components. For industries handling diverse goods—such as parcels in logistics or products in retail—the angle must be optimized to ensure seamless flow.
During conveyor belt installation, engineers assess the incline based on the type of material, belt design, and operational goals. For example, a steep incline might save floor space but could compromise stability, while a shallow angle might enhance control but require a longer conveyor. Balancing these factors is key to achieving efficiency.
What Are the Key Factors Influencing Conveyor Belt Angles?
Material Characteristics
The nature of the items being transported plays a significant role in conveyor belt installation design. Lightweight, smooth items like envelopes might handle steeper angles without slipping, while heavier or bulkier goods—like retail packages—require gentler slopes. The coefficient of friction between the belt surface and the material is a critical metric here. For instance, belts with textured surfaces or cleats can support steeper angles by preventing rollback, a feature often integrated into intelligent sorting systems.
The nature of the items being transported plays a significant role in conveyor belt installation design. Lightweight, smooth items like envelopes might handle steeper angles without slipping, while heavier or bulkier goods—like retail packages—require gentler slopes. The coefficient of friction between the belt surface and the material is a critical metric here. For instance, belts with textured surfaces or cleats can support steeper angles by preventing rollback, a feature often integrated into intelligent sorting systems.
Belt Design and Tension
The construction of the conveyor belt itself—whether modular, rubber, or fabric-based—impacts the feasible angle. During conveyor belt installation, tension must be carefully adjusted to maintain grip without overstressing the system. Overly steep angles can increase tension beyond the belt’s capacity, leading to premature wear or mechanical failure. Advanced systems, such as those used in e-commerce sorting, often employ belts with specialized coatings to optimize performance at varying inclines.
The construction of the conveyor belt itself—whether modular, rubber, or fabric-based—impacts the feasible angle. During conveyor belt installation, tension must be carefully adjusted to maintain grip without overstressing the system. Overly steep angles can increase tension beyond the belt’s capacity, leading to premature wear or mechanical failure. Advanced systems, such as those used in e-commerce sorting, often employ belts with specialized coatings to optimize performance at varying inclines.
Speed and Throughput Requirements
In high-speed sorting environments, such as courier express parcel hubs, the conveyor belt angle must align with operational tempo. A steep incline might slow down material flow due to gravity resistance, while a flat or slight incline can maintain momentum. Conveyor belt installation must account for how angle adjustments affect sorting accuracy and delivery timelines, especially in automated setups where sensors and diverters rely on consistent material positioning.
In high-speed sorting environments, such as courier express parcel hubs, the conveyor belt angle must align with operational tempo. A steep incline might slow down material flow due to gravity resistance, while a flat or slight incline can maintain momentum. Conveyor belt installation must account for how angle adjustments affect sorting accuracy and delivery timelines, especially in automated setups where sensors and diverters rely on consistent material positioning.
What Is the Industry Standard for Conveyor Belt Angles?
While there’s no one-size-fits-all answer, industry benchmarks provide a starting point for conveyor belt installation. For general-purpose conveying, inclines typically range from 0° (horizontal) to 20°. However, in specialized applications like intelligent sorting systems, angles can extend up to 30° or more with the right equipment.
- 0° to 10°: Ideal for fragile or loose items, ensuring minimal disruption. Common in wholesale and retail sorting.
- 10° to 20°: A versatile range for most packaged goods, balancing space efficiency and stability. Widely used in logistics operators.
- 20° to 30°: Suitable for compact systems with high-friction belts or cleats, often seen in e-commerce facilities with space constraints.
- Angles beyond 30° are rare without additional support mechanisms like sidewalls or custom belt designs, as slippage and energy costs rise significantly. During conveyor belt installation, testing the chosen angle under real-world loads is essential to validate performance.
How Does Conveyor Belt Installation Angle Affect Efficiency?
Energy Consumption
The steeper the angle, the more power a conveyor system requires to lift materials against gravity. In energy-conscious designs—common in modern logistics networks—engineers aim to minimize incline angles while meeting spatial needs. For example, a 15° incline might double the motor power demand compared to a flat belt, impacting long-term operational costs. Conveyor belt installation should thus prioritize angles that align with sustainability goals without sacrificing throughput.
The steeper the angle, the more power a conveyor system requires to lift materials against gravity. In energy-conscious designs—common in modern logistics networks—engineers aim to minimize incline angles while meeting spatial needs. For example, a 15° incline might double the motor power demand compared to a flat belt, impacting long-term operational costs. Conveyor belt installation should thus prioritize angles that align with sustainability goals without sacrificing throughput.
Space Optimization
In densely packed facilities, such as urban e-commerce warehouses, vertical space is a premium. A steeper conveyor belt angle can reduce the system’s footprint, allowing more room for sorting equipment or storage. However, this must be weighed against potential trade-offs in material control. Intelligent systems often integrate multi-tiered conveyors with moderate inclines (e.g., 15°–20°) to strike this balance.
In densely packed facilities, such as urban e-commerce warehouses, vertical space is a premium. A steeper conveyor belt angle can reduce the system’s footprint, allowing more room for sorting equipment or storage. However, this must be weighed against potential trade-offs in material control. Intelligent systems often integrate multi-tiered conveyors with moderate inclines (e.g., 15°–20°) to strike this balance.
Maintenance and Wear
Steep angles increase stress on belts, rollers, and motors, accelerating wear. Conveyor belt installation designs that push beyond recommended inclines may require more frequent retrofits or part replacements. In contrast, gentler slopes extend equipment lifespan, a key consideration for systems handling high volumes, like those in courier services.
Steep angles increase stress on belts, rollers, and motors, accelerating wear. Conveyor belt installation designs that push beyond recommended inclines may require more frequent retrofits or part replacements. In contrast, gentler slopes extend equipment lifespan, a key consideration for systems handling high volumes, like those in courier services.
What Are Best Practices for Conveyor Belt Installation Angles?
Conduct Material Testing
Before finalizing the angle, simulate material flow under various inclines. This step ensures the conveyor belt installation supports the specific goods—whether lightweight parcels or heavy wholesale items—without slippage or jams. Advanced sorting systems often use test runs to calibrate angles for peak efficiency.
Before finalizing the angle, simulate material flow under various inclines. This step ensures the conveyor belt installation supports the specific goods—whether lightweight parcels or heavy wholesale items—without slippage or jams. Advanced sorting systems often use test runs to calibrate angles for peak efficiency.
Incorporate Support Features
For angles above 15°, consider adding cleats, side guards, or textured surfaces to the belt. These enhancements, common in intelligent conveying solutions, stabilize materials and expand the range of viable inclines. During conveyor belt installation, these features should be tailored to the system’s purpose, such as high-speed parcel sorting.
For angles above 15°, consider adding cleats, side guards, or textured surfaces to the belt. These enhancements, common in intelligent conveying solutions, stabilize materials and expand the range of viable inclines. During conveyor belt installation, these features should be tailored to the system’s purpose, such as high-speed parcel sorting.
Leverage Automation and Sensors
In smart sorting systems, sensors can monitor material behavior in real time, adjusting belt speed or angle dynamically (if the system allows). This adaptability reduces the risks of steep inclines, ensuring consistent performance. Conveyor belt installation in such setups often integrates these technologies for precision and reliability.
In smart sorting systems, sensors can monitor material behavior in real time, adjusting belt speed or angle dynamically (if the system allows). This adaptability reduces the risks of steep inclines, ensuring consistent performance. Conveyor belt installation in such setups often integrates these technologies for precision and reliability.
How Do Real-World Applications Shape Conveyor Belt Angles?
In logistics, a courier hub might use a 10° incline to move parcels upward to a sorting platform, prioritizing speed and stability. Conversely, an e-commerce facility with limited floor spaaples highlight how conveyor belt installation adapts to operational context—whether it’s maximizing throughput, conserving energy, or fitting into tight layouts.
The evolution of intelligent sorting systems has also introduced hybrid designs, where conveyors transition between flat and inclined sections. This flexibility allows operators to fine-tune angles based on real-time needs, a trend gaining traction in China’s fast-growing logistics market.
Conclusion: Finding the Sweet Spot for Conveyor Belt Installation
Determining the best angle for conveyor belt installation is a blend of science, engineering, and practical insight. It requires understanding material dynamics, system design, and operational goals. While angles between 10° and 20° suit most applications, advanced sorting systems can push boundaries with the right technology. By prioritizing efficiency, stability, and adaptability, engineers can optimize conveyor performance for industries like logistics, e-commerce, and beyond—delivering value through smart infrastructure.
Comments