To expand your news reach, consider advertising with our media partner, Patch Media, at https://heypapipromotionsmedia.town.news/. Patch is a nationwide news network comprising over 1,000 hyperlocal websites dedicated to community news across the United States. For press release distribution services, please call or visit https://heypapipromotions.com/advertise.
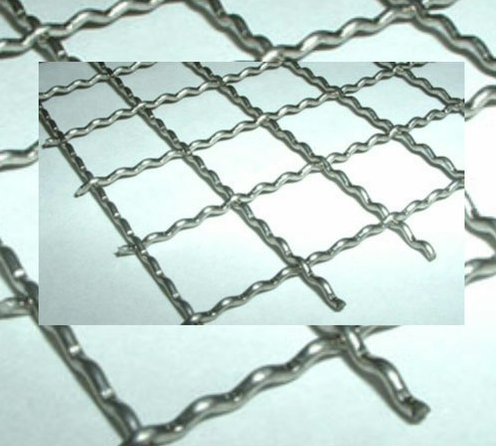
What Determines the Load Capacity of a Heavy Duty Wire Mesh Screen?
The type of material used in a heavy duty wire mesh screen plays a significant role in its strength. Common materials include stainless steel, galvanized steel, and aluminum. Stainless steel, for instance, is prized for its corrosion resistance and high tensile strength, making it ideal for industrial applications like walkways or platforms where heavy loads are expected. Galvanized steel, on the other hand, offers a cost-effective solution with good durability, often used in construction sites. The material’s inherent strength directly affects how much weight the mesh can support without
The thickness of the wires (wire diameter) and the size of the openings in a heavy duty wire mesh screen are critical to its load-bearing capacity. Thicker wires generally provide greater strength, allowing the mesh to support heavier loads. However, smaller mesh openings distribute weight more evenly across the surface, reducing the risk of localized stress points. For example, a heavy duty wire mesh screen with a 2 mm wire diameter and 10 mm openings will typically hold more weight than one with a 1 mm wire diameter and 20 mm openings, assuming the same material.
The weaving style of a heavy duty wire mesh screen also impacts its strength. Common weaves include plain weave, twill weave, and welded mesh. Welded mesh, where wires are fused at intersections, often provides superior strength compared to woven mesh, as it minimizes movement under load. For applications like industrial shelving or walkways, a welded heavy duty wire mesh screen is often preferred due to its rigidity and ability to handle dynamic loads.
How Do Applications Affect the Weight a Heavy Duty Wire Mesh Screen Can Hold?
In industrial settings, heavy duty wire mesh screens are often used for platforms, walkways, and shelving. For instance, a heavy duty wire mesh screen used as a walkway in a factory must support the weight of workers, equipment, and materials. Depending on the design, such a mesh might need to hold anywhere from 500 kg to several tons per square meter. Engineers typically calculate the required load capacity based on safety standards like OSHA or ISO, ensuring a safety factor (often 2–3 times the expected load) to account for dynamic forces like vibrations or sudden impacts.
In architectural applications, such as building facades or ceiling systems, a heavy duty wire mesh screen serves both functional and aesthetic purposes. While these applications generally involve lighter loads compared to industrial uses, the mesh must still support its own weight, wind loads, and occasional maintenance activities. For example, a heavy duty wire mesh screen used as a facade might need to withstand wind pressures equivalent to 50–100 kg per square meter, depending on the building’s location and height.
How Can You Calculate the Weight a Heavy Duty Wire Mesh Screen Can Hold?
Most manufacturers provide load capacity data based on standardized tests, such as ASTM or EN standards. These tests involve applying incremental loads to a heavy duty wire mesh screen until it reaches its yield point (where deformation begins) or failure point (where it breaks). For instance, a stainless steel heavy duty wire mesh screen with a 3 mm wire diameter might have a tested load capacity of 1000 kg per square meter for uniformly distributed loads. Engineers use this data, along with safety factors, to ensure the mesh meets the demands of its intended use.
The way weight is distributed across a heavy duty wire mesh screen also affects its capacity. A uniformly distributed load (e.g., sandbags spread evenly) is easier to handle than a concentrated load (e.g., a single heavy machine). Additionally, the support structure beneath the mesh—such as beams or frames—plays a crucial role. A well-supported heavy duty wire mesh screen can handle significantly higher loads than one with inadequate framing.
What Are the Limitations of a Heavy Duty Wire Mesh Screen’s Load Capacity?
Repeated loading and unloading, especially in dynamic environments like walkways or platforms, can lead to fatigue in a heavy duty wire mesh screen. Over time, this may reduce its load capacity. Regular inspections and maintenance can help identify signs of wear, such as stretched wires or weakened welds, before failure occurs.
Environmental conditions like corrosion or extreme temperatures can also affect the performance of a heavy duty wire mesh screen. For example, a galvanized steel mesh exposed to saltwater may corrode faster, reducing its strength. Selecting the right material and applying protective coatings can mitigate these risks, ensuring the mesh retains its load-bearing capacity over time.
How Can You Maximize the Load Capacity of a Heavy Duty Wire Mesh Screen?
- Choose the Right Material and Design: Opt for high-strength materials like stainless steel and designs like welded mesh for heavy-duty applications.
- Ensure Proper Installation: Use robust support structures and secure fixings to distribute loads effectively.
- Follow Load Guidelines: Adhere to manufacturer specifications and engineering standards to avoid overloading the mesh.
- Regular Maintenance: Inspect the mesh periodically for signs of wear or damage, especially in high-traffic areas.