Wax is divided into emulsion form, flake, and micronized wax. There is pure natural wax, modified natural wax, semi-synthetic wax, synthetic wax and so on. Powder coatings are mainly used for polymer modification and synthetic wax, and are solid, such as polyolefin wax and polytetrafluoroethylene (PTFE wax).
Frosting effect
When the melting point of the selected wax is lower than the baking temperature, because the wax melts into a liquid during baking, a thin layer similar to frost is formed on the coating surface after film cooling.
Axis effect
The effect is that the wax is exposed to the outside by its own particle size similar to or larger than the thickness of the coating film so that the scratch resistance and scratch resistance of the wax can be shown.
Floating effect
Regardless of the wax particle morphology, wax drifts to the surface of the film during film formation and disperses evenly, which makes the top layer of the film protected by wax and shows the characteristics of wax.
II. Application of micronized wax powder
Degassing
Because there are small molecular substances on the surface of powder coated substrates, especially in porous substrates such as cast iron, cast aluminum, and zinc substrates, this kind of wax solves coating defects such as pores, bubbles, and depressions caused by the above substrates.
Improving leveling
Some amino modified polyethylene waxes have better wettability in resin-coated fillers and pigments because they are of the same type as the leveling agents used in powder coatings. As a result, surface leveling also improves.
Increasing Smoothness of Powder
Basically, each kind of micronized wax powder has the effect of improving the smoothness of powder and increasing the storage stability of paint. Generally speaking, considering the cost, adding 0.2-0.5% (wt) in the formula, the micronized wax powder is more popular. It should be noted that the influence of the manufacturing process and impurities of low-grade wax on powder coatings cannot be ignored. More importantly, in addition to some wax formulations, when baking, odor and smoke are particularly large, which is not conducive to environmental protection and safety. Additionally, the raw material with a small amount of wax is not easy to stick to the cooling roll after extrusion.
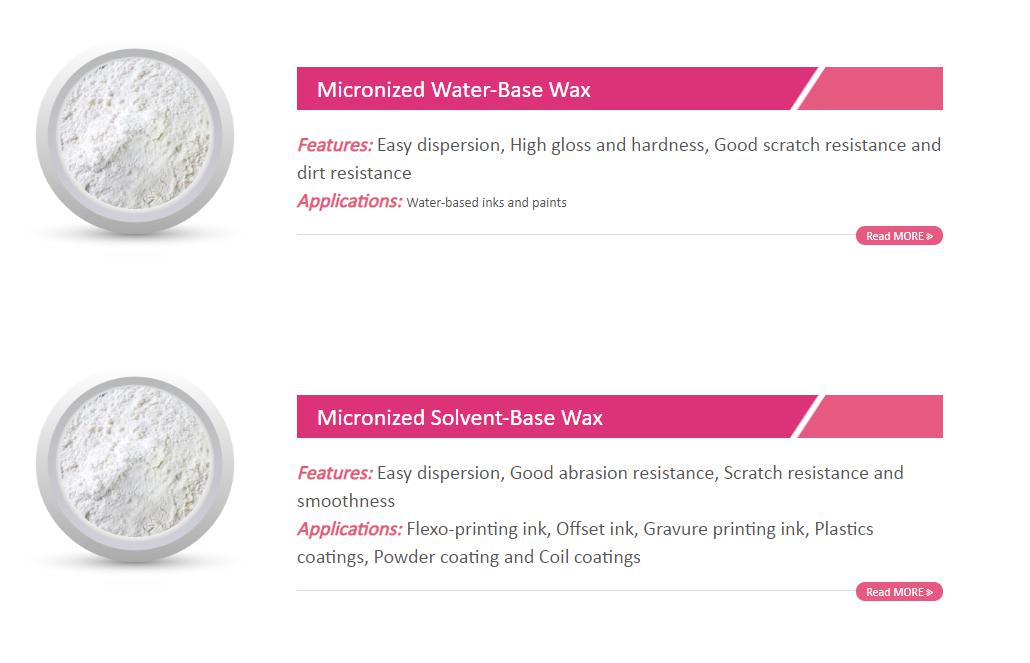
Controlling glossiness
There are two kinds of extinction: physical extinction and chemical extinction. The extinction of polyolefin wax belongs to the former. The wax will float to the surface of the film and form fog when baking, thus reducing the gloss. If a micronized wax powder is used alone, the dosage is 1.0-3.5% (wt). In such applications, micronized wax should be used as far as possible because it is easy to disperse. If wax sheets are used and added to 1.5% (wt), there will be a small dent on the surface of the coating. And after re-extrusion, the depression will only increase. Planar products generally add up to 3.5% (wt). If this amount is exceeded, the horizontal fluidity of powder melting decreases obviously. Moreover, the greater the wettability of the powder, the worse the changeability of the powder.
It is chemically resistant.
Due to the floating effect of wax, a compact oil bearing layer is formed on the surface of the coating, so the boiling water resistance is better, and the salt spray resistance is superior.
It is wear-resistant, scratch-proof and scratch-proof.
Wax is distributed on the surface of the film to protect the film, prevent scratches, scratches and provide wear resistance. Generally, propylene modified wax and polytetrafluoroethylene wax are added, especially for dark flat formula and low gloss sand grain formula.