To expand your news reach, consider advertising with our media partner, Patch Media, at https://heypapipromotionsmedia.town.news/. Patch is a nationwide news network comprising over 1,000 hyperlocal websites dedicated to community news across the United States. For press release distribution services, please call or visit https://heypapipromotions.com/advertise.
The air separation unit air liquide is a cornerstone of industrial gas production, delivering high-purity oxygen, nitrogen, and other gases for applications in industries like healthcare, metallurgy, and electronics. At the heart of this sophisticated system lies the main heat exchanger, a critical component that ensures the efficiency and reliability of the air separation process. This article explores the function, types, and significance of the main heat exchanger in an air separation unit air liquide, providing a detailed yet accessible overview for those interested in air separation technology.
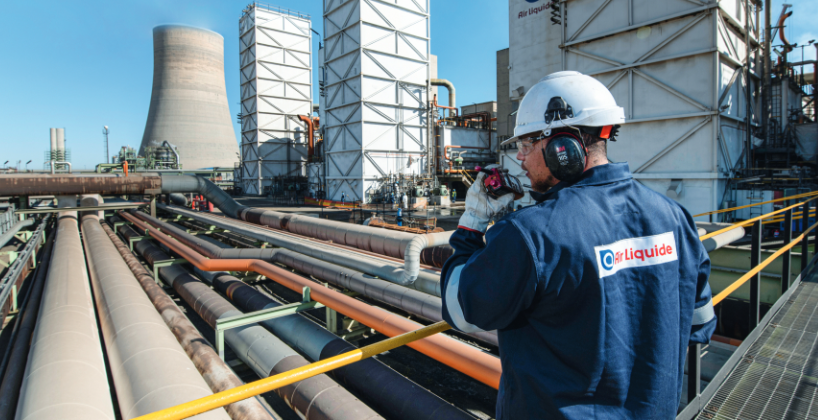
Understanding the Air Separation Unit Air Liquide
An air separation unit air liquide is designed to separate atmospheric air into its primary components—oxygen, nitrogen, and sometimes argon—through a process called cryogenic distillation or non-cryogenic methods like pressure swing adsorption (PSA). The cryogenic process, commonly used in large-scale air separation unit air liquide systems, relies on cooling air to extremely low temperatures to liquefy and separate its constituents based on their boiling points.
The main heat exchanger in an air separation unit air liquide facilitates this cooling by transferring heat between incoming air and cold product streams. Without an efficient heat exchanger, the energy costs of achieving the necessary low temperatures would be prohibitive, making the heat exchanger a pivotal element in the system’s design.
What Is the Main Heat Exchanger?
Definition and Function
- In an air separation unit air liquide, the main heat exchanger is a device that cools incoming atmospheric air by exchanging heat with cold gas streams, such as oxygen and nitrogen, produced during the separation process. This heat transfer reduces the temperature of the incoming air to near its liquefaction point, preparing it for distillation in the air separation unit air liquide’s columns.
- The heat exchanger operates on the principle of countercurrent flow, where warm air flows in one direction and cold product gases flow in the opposite direction. This setup maximizes heat transfer efficiency, ensuring that the air separation unit air liquide consumes minimal energy to achieve the required cryogenic temperatures.
Importance in Energy Efficiency
- Energy efficiency is a critical concern in any air separation unit air liquide, as cooling air to temperatures below -190°C demands significant energy input. The main heat exchanger minimizes this energy requirement by recovering cold energy from the product gases and using it to pre-cool the incoming air. This process, known as recuperative heat exchange, is essential for making large-scale air separation unit air liquide systems economically viable.
Types of Main Heat Exchangers in Air Separation Unit Air Liquide Systems
Several types of heat exchangers are used in an air separation unit air liquide, each suited to specific operational needs. The choice of heat exchanger depends on factors like plant size, production capacity, and the desired purity of the output gases.
Plate-Fin Heat Exchangers
- The most common type in an air separation unit air liquide is the plate-fin heat exchanger. This compact design consists of stacked aluminum plates and fins that create multiple flow channels for air and product gases. Plate-fin heat exchangers are highly efficient due to their large surface area, making them ideal for large-scale air separation unit air liquide systems that produce liquid oxygen or nitrogen.
- Their robust construction also allows them to withstand the thermal stresses caused by extreme temperature differences, a common challenge in cryogenic air separation unit air liquide operations.
Shell-and-Tube Heat Exchangers
- Although less common in modern air separation unit air liquide systems, shell-and-tube heat exchangers are sometimes used in smaller or specialized plants. These consist of a series of tubes through which one fluid flows, surrounded by a shell containing another fluid. While durable, they are less efficient than plate-fin designs and are typically reserved for applications with lower throughput.
Coil-Wound Heat Exchangers
- Coil-wound heat exchangers are another option in an air separation unit air liquide, particularly for very large plants. These consist of multiple tube bundles wound in a helical pattern, allowing for high heat transfer efficiency and the ability to handle large flow rates. Their complex design makes them more expensive, but they are well-suited for high-capacity air separation unit air liquide systems.
How Does the Main Heat Exchanger Enhance Air Separation Unit Air Liquide Performance?
Temperature Control and Stability
- The main heat exchanger ensures precise temperature control in an air separation unit air liquide, which is critical for maintaining the efficiency of the distillation process. By cooling the incoming air uniformly, it prevents fluctuations that could disrupt the separation of oxygen and nitrogen, ensuring consistent product purity.
Integration with Other Components
- In an air separation unit air liquide, the heat exchanger works in tandem with other components like compressors, turbines, and distillation columns. For example, compressed air from the purification system enters the heat exchanger, where it is cooled before being fed into the distillation column. This integration optimizes the overall performance of the air separation unit air liquide.
Adaptability to Diverse Applications
- The versatility of the main heat exchanger allows an air separation unit air liquide to meet diverse industry needs. Whether producing gaseous oxygen for medical use or liquid nitrogen for industrial cooling, the heat exchanger can be tailored to handle varying flow rates and temperature requirements, making it a key enabler of flexible production.
Challenges and Innovations in Heat Exchanger Design
Managing Thermal Stress
- One of the primary challenges in an air separation unit air liquide is managing thermal stress in the heat exchanger. The extreme temperature gradients between incoming air and cold product gases can cause material fatigue over time. Advances in materials science, such as the use of high-strength aluminum alloys, have improved the durability of heat exchangers in air separation unit air liquide systems.
Preventing Contamination
- Contamination is another concern, as impurities like moisture or hydrocarbons in the incoming air can freeze and clog the heat exchanger. Modern air separation unit air liquide systems incorporate advanced air purification systems, including filters and dryers, to ensure clean air enters the heat exchanger, reducing maintenance needs.
Innovations in Efficiency
- Recent innovations focus on enhancing the efficiency of heat exchangers in an air separation unit air liquide. For instance, improved fin designs and optimized flow patterns increase heat transfer rates, while smart control systems monitor and adjust operating conditions in real time. These advancements contribute to lower energy consumption and higher reliability.
The Future of Heat Exchangers in Air Separation Unit Air Liquide Technology
As industries demand greener and more efficient solutions, the role of the main heat exchanger in an air separation unit air liquide will continue to evolve. Emerging trends include the integration of digital monitoring systems to predict maintenance needs and the development of hybrid heat exchanger designs that combine the benefits of plate-fin and coil-wound technologies.
Moreover, as air separation unit air liquide systems expand into new markets—like renewable energy and carbon capture—heat exchangers will need to adapt to new operational challenges, such as handling non-traditional gas mixtures or operating in extreme environments.
Conclusion
The main heat exchanger is an unsung hero in the air separation unit air liquide, enabling the efficient production of vital industrial gases like oxygen and nitrogen. By facilitating precise temperature control and energy recovery, it ensures that air separation processes are both cost-effective and reliable. As technology advances, the heat exchanger will remain a focal point for innovation, driving improvements in the performance and sustainability of air separation unit air liquide systems worldwide.
Comments