To expand your news reach, consider advertising with our media partner, Patch Media, at https://heypapipromotionsmedia.town.news/. Patch is a nationwide news network comprising over 1,000 hyperlocal websites dedicated to community news across the United States. For press release distribution services, please call or visit https://heypapipromotions.com/advertise.
Oxygen is essential for countless industries, from healthcare to manufacturing, and producing it efficiently requires advanced technology. Among the many solutions available, the cryogenic oxygen plant stands out as a cornerstone of the air separation industry. These plants use low-temperature distillation to separate air into its primary components—oxygen, nitrogen, and other gases—offering high purity and large-scale output. Let’s dive into why these systems, alongside other technologies, are some of the best for oxygen production and how they align with modern industrial demands.
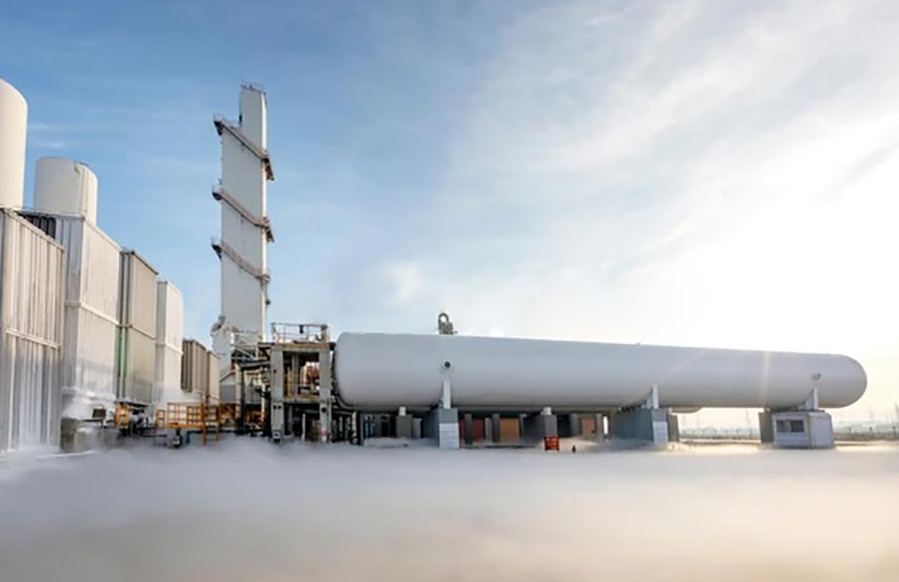
How Do Cryogenic Oxygen Plants Work?
A cryogenic oxygen plant operates by cooling air to extremely low temperatures, typically below -195°C (-319°F), where it liquefies. This process leverages the different boiling points of oxygen (-183°C) and nitrogen (-195.8°C) to separate them through fractional distillation. The result? Oxygen with purity levels often exceeding 99%, making it ideal for applications like steel production, chemical manufacturing, and medical use.
The process begins with air compression, followed by purification to remove impurities like water vapor and carbon dioxide. The cleaned air is then cooled in heat exchangers and distilled in a column, producing liquid oxygen that can be stored or vaporized as needed. This scalability and precision make cryogenic oxygen plants a go-to for industries requiring consistent, high-volume oxygen supply.
Why Are Cryogenic Oxygen Plants So Effective?
The effectiveness of a cryogenic oxygen plant lies in its ability to handle large-scale production while maintaining exceptional purity. For instance, a single plant can produce thousands of cubic meters of oxygen per hour, meeting the needs of massive operations like metal smelting or petrochemical refining. Additionally, these plants can co-produce nitrogen and argon, adding versatility to their output.
Their global application is evident in projects like those in Russia, where cryogenic oxygen plants support industrial growth with reliable oxygen supply. This efficiency and adaptability make them a benchmark in the air separation field, though they require significant infrastructure and energy, which we’ll explore later.
How Do PSA Oxygen Generators Compare to Cryogenic Oxygen Plants?
While cryogenic oxygen plants excel in large-scale production, Pressure Swing Adsorption (PSA) oxygen generators offer a different approach, particularly for smaller or mid-sized operations. These systems use adsorbent materials, like zeolites, to selectively trap nitrogen from compressed air, releasing oxygen as the primary output.
The Mechanics of PSA Oxygen Generators
In a PSA system, air is compressed and passed through an adsorbent bed. Nitrogen molecules are captured due to their stronger affinity for the adsorbent, while oxygen passes through. The process alternates between two beds—one adsorbing while the other regenerates—ensuring a continuous flow. Purity levels typically reach 90-95%, sufficient for applications like wastewater treatment or fish farming.
For example, PSA nitrogen generators in Thailand demonstrate how this technology adapts to specific regional needs, offering a compact, cost-effective alternative to cryogenic oxygen plants. Unlike cryogenic systems, PSA units don’t require extreme cooling, making them simpler to install and maintain.
When to Choose PSA Over Cryogenic Systems
PSA oxygen generators shine in scenarios where mobility, lower energy use, or moderate oxygen volumes are priorities. They’re less suited for ultra-high-purity needs compared to a cryogenic oxygen plant, but their flexibility makes them invaluable in industries like food packaging or small-scale medical facilities. The choice depends on scale, purity requirements, and operational context.
What Role Do Low-Temperature Storage Tanks Play in Oxygen Production?
Producing oxygen is only half the equation—storing and distributing it efficiently is equally critical. Low-temperature storage tanks, often paired with cryogenic oxygen plants, ensure that liquid oxygen remains stable and ready for use. These tanks maintain oxygen at temperatures below -183°C, preventing evaporation and enabling long-term storage.
Applications of Low-Temperature Storage Tanks
In Turkey, liquid oxygen storage tanks support gas stations, showcasing their role in bridging production and end-use. These tanks are engineered with vacuum insulation to minimize heat transfer, preserving the cryogenic state of oxygen or nitrogen. They’re essential for industries needing a steady supply without constant production, such as hospitals or aerospace manufacturing.
Pairing these tanks with a cryogenic oxygen plant creates a seamless system: the plant produces liquid oxygen, and the tanks store it until vaporized for delivery. This synergy enhances operational efficiency, especially in remote or high-demand settings.
How Do Supporting Technologies Enhance Oxygen Production?
Beyond core systems like cryogenic oxygen plants and PSA generators, auxiliary components play a vital role in optimizing oxygen production. Compressed air purification systems and filters, for instance, ensure that input air is free of contaminants, protecting equipment and improving output quality.
The Importance of Air Purification
Before air enters a cryogenic oxygen plant or PSA unit, it must be purified to remove moisture, oil, and particulates. This step prevents damage to sensitive components, like distillation columns or adsorbents, and ensures the final oxygen meets purity standards. In South Africa, oil-free compressors paired with air separation systems exemplify how clean input air boosts reliability.
Intelligent Control Valves: Precision in Action
Advanced production lines for intelligent control valves, another key offering, allow precise regulation of gas flow and pressure. These valves enhance the performance of cryogenic oxygen plants by minimizing waste and optimizing energy use, a critical factor given the energy-intensive nature of cryogenic processes.
What Are the Best Plants for Your Oxygen Needs?
Choosing the “best” oxygen-producing plant depends on your specific requirements. A cryogenic oxygen plant is unmatched for high-purity, large-scale production, as seen in global projects from Russia to Chile. PSA generators offer flexibility and lower costs for smaller operations, while low-temperature storage tanks ensure supply stability.
Balancing Efficiency and Application
For industries like steelmaking, the energy investment in a cryogenic oxygen plant pays off with its capacity and purity. Conversely, a containerized PSA oxygen generator in Chile highlights how portability can serve remote healthcare needs. Each technology has its niche, shaped by factors like volume, location, and end-use.
Looking Ahead in Air Separation
As demand for oxygen and nitrogen grows, innovations in energy efficiency and modular design will likely refine these systems further. Whether through a cryogenic oxygen plant or a hybrid approach, the air separation industry continues to evolve, offering tailored solutions for a world that runs on air.
Comments