If you're new to the world of electronics, you've likely come across the term "soldering." Soldering is a crucial technique for creating connections and integrating components into circuit boards. However, to perform soldering tasks, you'll need the right equipment. While soldering machines are widely used, determining the best type for your project can be daunting.
In this article, we'll delve into the various types of soldering machines and their functionalities. Additionally, we'll provide a refresher on what solder machines are and how they operate, making it easier for you to choose the right equipment for your soldering needs.
What Is Soldering Machine?
A soldering machine is a specialized tool used in electronics assembly and repair processes. It is designed to join electronic components together by melting solder, a metal alloy with a low melting point, and creating a strong electrical and mechanical bond between them. Soldering machines come in various types and configurations, ranging from simple handheld soldering irons to advanced automated soldering systems used in manufacturing environments.
At its core, a soldering machine typically consists of a heating element, a tip or nozzle for applying heat to the solder joint, and a control mechanism to regulate temperature and other parameters. The heating element can be powered by electricity, gas, or induction, depending on the type of soldering machine.
Soldering machines are widely used in various industries, including electronics manufacturing, automotive, aerospace, and telecommunications. They play a critical role in assembling printed circuit boards (PCBs), soldering surface-mount components, wire splicing, and repairing electronic devices.
Types of Soldering Machines
Soldering machines come in various types, each tailored to specific applications and requirements in electronics assembly and repair. Here are some common types of soldering machines:
1.Soldering Iron
Handheld soldering irons are one of the most basic and widely used types of soldering machines.
They consist of a heated metal tip connected to a handle and are powered by electricity.
Soldering irons are versatile and suitable for a wide range of soldering tasks, from simple repairs to intricate circuit board assembly.
They consist of a heated metal tip connected to a handle and are powered by electricity.
Soldering irons are versatile and suitable for a wide range of soldering tasks, from simple repairs to intricate circuit board assembly.
2.Soldering Station
A soldering station is a more advanced version of a soldering iron, typically featuring temperature control and additional features such as interchangeable tips and digital displays.
Soldering stations offer improved precision and consistency in temperature regulation, making them ideal for professional and high-volume soldering applications.
Soldering stations offer improved precision and consistency in temperature regulation, making them ideal for professional and high-volume soldering applications.
3.Hot Air Rework Station
Hot air rework stations use a stream of heated air to melt solder and remove or replace surface-mount components on circuit boards.
They are commonly used for tasks such as desoldering and reflowing surface-mount components like integrated circuits (ICs), resistors, and capacitors.
They are commonly used for tasks such as desoldering and reflowing surface-mount components like integrated circuits (ICs), resistors, and capacitors.
4.Soldering Robot
Soldering robots, also known as automated soldering systems, are programmable machines equipped with robotic arms and soldering heads.
These machines are used in high-volume manufacturing environments to automate the soldering process, improving efficiency and consistency while reducing labor costs.
These machines are used in high-volume manufacturing environments to automate the soldering process, improving efficiency and consistency while reducing labor costs.
.Wave Soldering Machine
Wave soldering machines are used in large-scale electronics manufacturing to solder through-hole components on printed circuit boards (PCBs).
These machines employ a conveyor system to move PCBs over a wave of molten solder, ensuring efficient and uniform soldering of components.
These machines employ a conveyor system to move PCBs over a wave of molten solder, ensuring efficient and uniform soldering of components.
6.Reflow Soldering Oven
Reflow soldering ovens are used in surface-mount technology (SMT) assembly processes to solder surface-mount components onto PCBs.
These ovens utilize controlled heating and cooling cycles to melt solder paste and create reliable solder joints between components and PCB pads.
These ovens utilize controlled heating and cooling cycles to melt solder paste and create reliable solder joints between components and PCB pads.
7.Ultrasonic Soldering Machine
Ultrasonic soldering machines utilize high-frequency vibrations to create frictional heat at the solder joint, enabling rapid soldering of small components and delicate materials.
These machines are often used for precision soldering applications in industries such as microelectronics and medical device manufacturing.
These machines are often used for precision soldering applications in industries such as microelectronics and medical device manufacturing.
Wave Soldering Machine
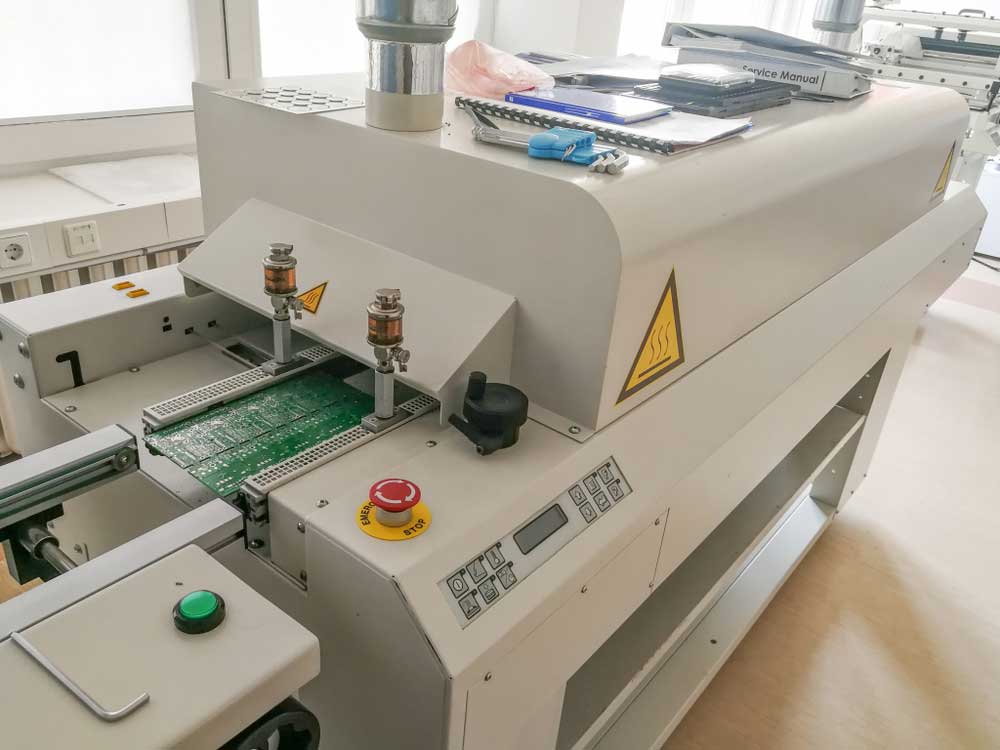
Many PCB manufacturers utilize wave soldering for large-scale PCB assembly, as it allows for the rapid soldering of boards with both leaded and surface-mount device (SMD) components. However, this method requires specialized machinery to execute efficiently.
Enter the wave soldering machine. This equipment features a heated tank of solder that remains in a molten state, ready for use at all times. The solder tank is maintained at an optimal temperature to ensure the solder remains melted and primed for the soldering process.
But how does this machine operate? Inside the tank, a wave of solder is generated, providing manufacturers with a consistent flow of solder to apply to circuit boards. As the boards pass through the wave soldering machine, only their underside comes into contact with the solder wave.
However, this process demands careful attention, particularly when adjusting the height of the solder wave. It must be precisely calibrated to prevent solder overflow, which could lead to unwanted solder reaching areas of the board that do not require soldering.
Furthermore, to secure the PCBs on the conveyor during the soldering process, metal fingers are employed. These fingers, typically crafted from titanium, are designed to withstand the high temperatures generated by the soldering machine, ensuring the boards remain securely in place throughout the assembly process.
Preparation
Preparation
To prepare for wave soldering, several key steps must be followed to ensure optimal results. Here's a breakdown of the process:
1.Apply Solder Resist Layer:
Before wave soldering, apply a solder resist layer to the circuit board. This layer, resembling varnish, prevents solder from adhering to the surface. Leave only the areas where solder exposure is desired uncovered.
2.Ensure Adequate Spacing:
Verify that there is sufficient spacing between solder pads on the board. Inadequate spacing may result in solder bridges, compromising the integrity of the solder joints.
3.Clean Solderable Areas:
Prior to soldering, ensure that the solderable areas are clean and free from oxidation. This can be achieved by using foam or spray flux to remove any contaminants and promote proper solder adhesion.
4.Preheat the Board:
Before introducing the board to the wave soldering machine, preheat it to mitigate thermal shocks. Extreme temperature differentials can lead to damage or defects in the components or circuitry.
5.Wave Soldering Process:
Once the board is adequately prepared, pass it through the wave soldering machine. This machine subjects the board to high temperatures, causing the solder to flow and create solder joints on the exposed areas.
By following these steps meticulously, you can ensure a successful wave soldering process, resulting in high-quality solder joints and reliable circuit board assembly.
1.Apply Solder Resist Layer:
Before wave soldering, apply a solder resist layer to the circuit board. This layer, resembling varnish, prevents solder from adhering to the surface. Leave only the areas where solder exposure is desired uncovered.
2.Ensure Adequate Spacing:
Verify that there is sufficient spacing between solder pads on the board. Inadequate spacing may result in solder bridges, compromising the integrity of the solder joints.
3.Clean Solderable Areas:
Prior to soldering, ensure that the solderable areas are clean and free from oxidation. This can be achieved by using foam or spray flux to remove any contaminants and promote proper solder adhesion.
4.Preheat the Board:
Before introducing the board to the wave soldering machine, preheat it to mitigate thermal shocks. Extreme temperature differentials can lead to damage or defects in the components or circuitry.
5.Wave Soldering Process:
Once the board is adequately prepared, pass it through the wave soldering machine. This machine subjects the board to high temperatures, causing the solder to flow and create solder joints on the exposed areas.
By following these steps meticulously, you can ensure a successful wave soldering process, resulting in high-quality solder joints and reliable circuit board assembly.
Reflow Soldering Machine
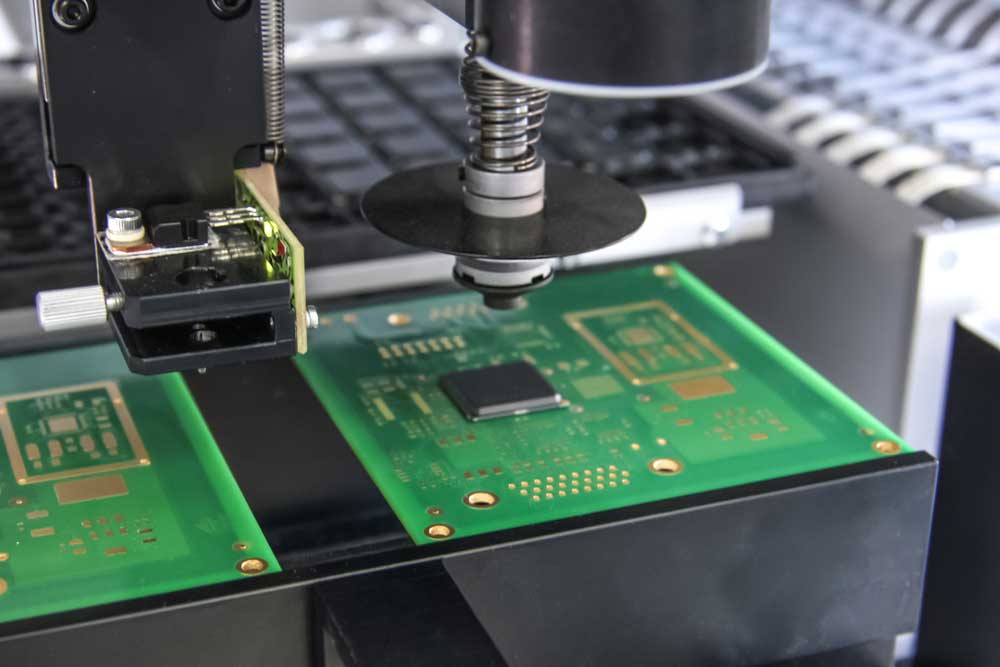
A reflow soldering machine functions as an oven, commonly employed in PCB assembly and production processes due to its widespread use. These machines, varying in size, provide soldering capabilities for both small-scale and large-scale assembly tasks.
Smaller versions of reflow soldering machines cater to minor rework and prototype areas but lack the soldering capacity of larger models.
Reflow soldering operates on the principle of applying solder paste to desired areas on the board, placing components, and then subjecting the assembly to controlled heating within a tunnel.
The controlled heat within the tunnel ensures the solder melts and secures the components without causing damage to the board.
Reflow soldering machines stand out as one of the most dependable methods for connecting SMD components.
Smaller versions of reflow soldering machines cater to minor rework and prototype areas but lack the soldering capacity of larger models.
Reflow soldering operates on the principle of applying solder paste to desired areas on the board, placing components, and then subjecting the assembly to controlled heating within a tunnel.
The controlled heat within the tunnel ensures the solder melts and secures the components without causing damage to the board.
Reflow soldering machines stand out as one of the most dependable methods for connecting SMD components.
Preparation
The initial step involves applying solder paste and affixing components onto your PCB. It's crucial to only apply solder where necessary, a task made easier with the assistance of a soldering paste and mask machine.
Once the paste is applied, utilize a pick and place machine for precise component positioning on the board. The surface tension of the paste ensures firm adhesion. Subsequently, the board is passed through the reflow soldering machine.
Gradually elevate the board's temperature to the designated level. Rapid heating may lead to uneven distribution, while excessively slow heating may fail to reach the required temperature. The recommended temperature increase rate is 2 to 3 degrees per second.
Upon reaching the target temperature, the process enters the thermal soak stage to ensure uniform temperature distribution. The reflow process commences when the board achieves the maximum temperature, facilitating solder melting and joint formation.
Finally, the board undergoes cooling within a temperature range of 30 to 100 degrees Celsius.
Once the paste is applied, utilize a pick and place machine for precise component positioning on the board. The surface tension of the paste ensures firm adhesion. Subsequently, the board is passed through the reflow soldering machine.
Gradually elevate the board's temperature to the designated level. Rapid heating may lead to uneven distribution, while excessively slow heating may fail to reach the required temperature. The recommended temperature increase rate is 2 to 3 degrees per second.
Upon reaching the target temperature, the process enters the thermal soak stage to ensure uniform temperature distribution. The reflow process commences when the board achieves the maximum temperature, facilitating solder melting and joint formation.
Finally, the board undergoes cooling within a temperature range of 30 to 100 degrees Celsius.
Final Words
When discussing soldering, our minds often envision the conventional soldering iron or pencil. However, for PCB manufacturers dealing with mass production, selling individual PCBs isn't feasible. Instead, they employ advanced techniques and machinery.
Two primary soldering methods are wave and reflow soldering. Wave soldering utilizes melted solder stored in a tank, whereas reflow soldering employs an oven-like mechanism to melt solder paste applied to the PCB.
If you have any inquiries, don't hesitate to contact us. We're here to assist you.
Comments