To expand your news reach, consider advertising with our media partner, Patch Media, at https://heypapipromotionsmedia.town.news/. Patch is a nationwide news network comprising over 1,000 hyperlocal websites dedicated to community news across the United States. For press release distribution services, please call or visit https://heypapipromotions.com/advertise.
Solar power systems offer an eco-friendly and cost-effective way to harness the energy of the sun and convert it into usable electricity. Whether you're considering solar panels for your home or a remote off-grid installation, solar charge controllers play a vital role in ensuring the efficiency and longevity of your system. In this article, we'll explore how solar charge controllers work and the various types available to help you make informed decisions for your solar project.
How Does a Solar Charge Controller Work?
The first solar charge controller schematic, depicted in Figure 1, illustrates the connection of a solar charge controller to power a direct current (DC) load. The second schematic, shown in Figure 2, pertains to an alternating current (AC) load.
Figure 1: Off-grid Diagram with DC Load
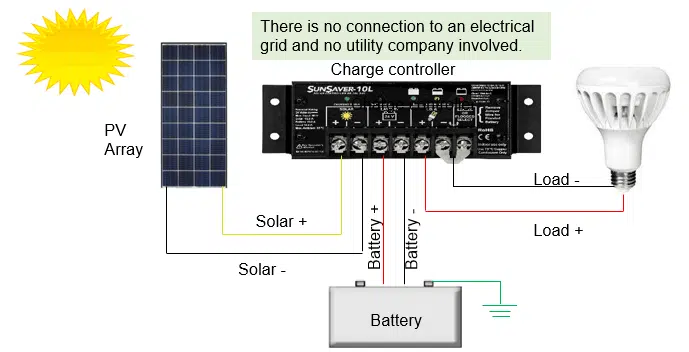
When installing a solar charge controller, it is advisable to follow a specific order for connecting and disconnecting:
- Connect the battery to the controller first.
- Connect the PV array to the controller.
- Connect the electrical load to the controller.
When disconnecting, you should reverse this order. The battery supplies power to the controller, so always ensure that the solar panels and loads are disconnected before connecting or disconnecting the battery from the controller. To enhance safety and simplify installation and breakdown, it's recommended to have disconnect switches in the connections between the battery, load, PV array, and the controller.
In the wire diagram schematic with a DC load, sunlight reaches the solar modules, which convert solar energy into DC electrical power. This power is then delivered to a charge controller. The charge controller regulates the amperage and voltage supplied to the loads, and any excess power is directed to the battery system to maintain the state of charge without overcharging. During the evening when there is no sunlight, battery power is used to operate the load.
You may notice that the battery is grounded at the negative battery terminal. This is because all our PWM and MPPT controllers share a common negative ground. Therefore, it is possible to establish a common negative ground for the entire system, including the solar array, controller, battery, and load. This configuration complies with NEC code requirements for grounding. For controllers that lack an equipment ground terminal lug, you can directly connect an equipment ground to the controller enclosure for any metal parts.
Figure 2: Off-grid Diagram with AC Load
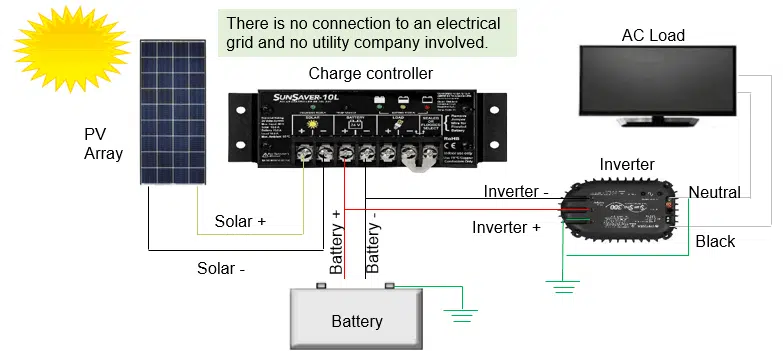
The next diagram, as seen in Figure 2, illustrates the components and connections required to power an AC load. This schematic with an AC load closely resembles the previous DC load example. However, in this scenario, an inverter has been added to the system. The inverter's role is to convert DC power from the battery into AC power, which can be utilized to operate AC loads, such as the TV shown in the schematic.
It's important to note that the inverter is connected and powered directly from the battery, not from the controller's load terminals, as in the DC load example. This arrangement is necessary because inverters can produce a high energy surge during startup, and this surge may exceed the rated capacity of the charge controller. Batteries, on the other hand, can meet the high-energy surge requirement.
Charge Controller Types:PWM Vs MPPT
It can be seen from the chart below that PWM controllers operate at battery voltage and are smaller, while MPPT controllers operate at maximum power voltage using newer technology. As a result, the array voltage gets increasingly higher than the battery voltage in colder conditions, maximizing the amount of power being produced. Moreover, MPPT controllers can operate at higher voltages and lower array currents, which can result in fewer strings in parallel and smaller wire sizes.
A PWM controller can only be used with arrays matched to the battery voltage, so what modules can be used are limited. Many 60 cell modules have a maximum power voltage (Vmp) equal to about 30V, making them suitable for MPPT controllers, but not PWM controllers.
In short, what's better, PWM or MPPT? All things being equal, MPPT is the newer technology that harvests a greater amount of energy. Despite MPPT's advantages, it is not always a smart choice to choose a PWM controller, especially for smaller systems or in warm climates where MPPT boosts are less noticeable.
PWM vs. MPPT Solar Charge Controller Comparison
PWM Controllers | MPPT Controllers |
Array voltage is “pulled down” to battery voltage | Convert excess input voltage into amperage |
Generally operate below Vmp | Operate at Vmp |
Suitable for small module configurations | Suitable for large module configurations that have a lower cost per watt |
Often chosen for very hot climates which will not yield as much MPPT boost | Provide more boost than PWM, especially during cold days and/or when the battery voltage is low |
PWM Charging
Conventional solar regulators featuring PWM (Pulse Width Modulation) charging function by creating a direct connection from the solar array to the battery bank. During the bulk charging phase, when there is an uninterrupted connection from the array to the battery bank, the array's output voltage aligns with the battery voltage. The battery voltage undergoes slight adjustments based on the array's current supply and the battery's size and characteristics.
MPPT Charging
Morningstar MPPT controllers incorporate TrakStar technology, which is engineered to swiftly and precisely determine the Vmp (maximum power voltage) of the solar array. TrakStar MPPT controllers employ a technique where they 'sweep' the solar input to identify the voltage at which the array produces the maximum power. The controller captures power from the array at this Vmp voltage and converts it to the battery voltage, simultaneously boosting the charging current.
Why Choose PWM Over MPPT
The comparison between PWM and MPPT may raise questions about why one would opt for a PWM controller over an MPPT controller. Several factors may reduce or negate the advantages provided by MPPT controllers. Considerations should include the cost, as MPPT controllers generally come at a higher price point than their PWM counterparts. When deciding on a controller, it's essential to assess the additional cost of MPPT in relation to the following factors:
Low Power Applications: Low power, specifically low current charging applications, might achieve similar or even superior energy harvest with a PWM controller. PWM controllers maintain relatively consistent harvesting efficiency regardless of the system's size. In contrast, MPPT regulators may exhibit reduced harvesting efficiency when used in low- power applications. It's crucial to review efficiency curves available in Morningstar MPPT controller manuals when making a regulator selection.
Climate Considerations: The most significant benefit of an MPPT regulator is often observed in colder climates where Vmp (voltage at maximum power) is higher. Conversely, in hotter climates, Vmp decreases, reducing MPPT harvest compared to PWM. High average ambient temperatures at the installation site may render the advantages of MPPT less economical.
Full Battery Conditions: Systems in which the solar array's power output significantly exceeds the power draw of the system's loads may result in the batteries remaining at full or near-full charge most of the time. In such cases, the increased harvesting capability of an MPPT regulator may be unnecessary, especially if autonomy is not a critical factor.
Low Power Applications: Low power, specifically low current charging applications, might achieve similar or even superior energy harvest with a PWM controller. PWM controllers maintain relatively consistent harvesting efficiency regardless of the system's size. In contrast, MPPT regulators may exhibit reduced harvesting efficiency when used in low- power applications. It's crucial to review efficiency curves available in Morningstar MPPT controller manuals when making a regulator selection.
Climate Considerations: The most significant benefit of an MPPT regulator is often observed in colder climates where Vmp (voltage at maximum power) is higher. Conversely, in hotter climates, Vmp decreases, reducing MPPT harvest compared to PWM. High average ambient temperatures at the installation site may render the advantages of MPPT less economical.
Full Battery Conditions: Systems in which the solar array's power output significantly exceeds the power draw of the system's loads may result in the batteries remaining at full or near-full charge most of the time. In such cases, the increased harvesting capability of an MPPT regulator may be unnecessary, especially if autonomy is not a critical factor.
Why Choose MPPT Over PWM
Opting for MPPT controllers offers several advantages:
Increased Energy Harvest: MPPT controllers operate at array voltages above battery voltage, enhancing the energy harvest from solar arrays by 5 to 30% compared to PWM controllers, depending on climate conditions. The array's voltage and amperage are continually adjusted throughout the day to maximize power output.
Less Module Restrictions: MPPT controllers, operating arrays at voltages higher than battery voltage, can be used with a broader range of solar modules and array configurations. They can also support systems with smaller wire sizes.
Support for Oversized Arrays: Unlike PWM controllers, MPPT controllers can accommodate oversized arrays that might otherwise surpass the maximum power limits of the charge controller. The controller manages this by limiting the array's current intake during periods of high solar energy supply, usually in the middle of the day. While excess energy from the array is regulated during this time, oversized arrays can deliver more power during the early and late parts of the day, compared to smaller non-oversized arrays.
Increased Energy Harvest: MPPT controllers operate at array voltages above battery voltage, enhancing the energy harvest from solar arrays by 5 to 30% compared to PWM controllers, depending on climate conditions. The array's voltage and amperage are continually adjusted throughout the day to maximize power output.
Less Module Restrictions: MPPT controllers, operating arrays at voltages higher than battery voltage, can be used with a broader range of solar modules and array configurations. They can also support systems with smaller wire sizes.
Support for Oversized Arrays: Unlike PWM controllers, MPPT controllers can accommodate oversized arrays that might otherwise surpass the maximum power limits of the charge controller. The controller manages this by limiting the array's current intake during periods of high solar energy supply, usually in the middle of the day. While excess energy from the array is regulated during this time, oversized arrays can deliver more power during the early and late parts of the day, compared to smaller non-oversized arrays.
Comments