To expand your news reach, consider advertising with our media partner, Patch Media, at https://heypapipromotionsmedia.town.news/. Patch is a nationwide news network comprising over 1,000 hyperlocal websites dedicated to community news across the United States. For press release distribution services, please call or visit https://heypapipromotions.com/advertise.
An essential process in the electronics industry, solder reflow involves attaching surface-mounted components to printed circuit boards (PCBs) using solder paste. As a result, components are placed on a PCB, solder paste is applied to specific areas on the board, and then the assembly is heated in a reflow oven. As the solder paste melts, the component and the PCB are connected electrically and mechanically. In electronic products, the quality of the connections has a direct impact on their performance and reliability.
The solder reflow process is influenced by a variety of factors, including the composition of the solder paste, the type of reflow oven, and the temperature profile of the solder joint. In order to achieve optimal soldering results, it is essential that you understand these factors and how they interact. We are going to take a closer look at the solder reflow temperature curve in this article. It can be divided into four phases/zones that can be distinguished between the main temperature changes associated with the soldering temperature curve.
The solder reflow process is influenced by a variety of factors, including the composition of the solder paste, the type of reflow oven, and the temperature profile of the solder joint. In order to achieve optimal soldering results, it is essential that you understand these factors and how they interact. We are going to take a closer look at the solder reflow temperature curve in this article. It can be divided into four phases/zones that can be distinguished between the main temperature changes associated with the soldering temperature curve.
SMT Solder ReflowTemperature Curve
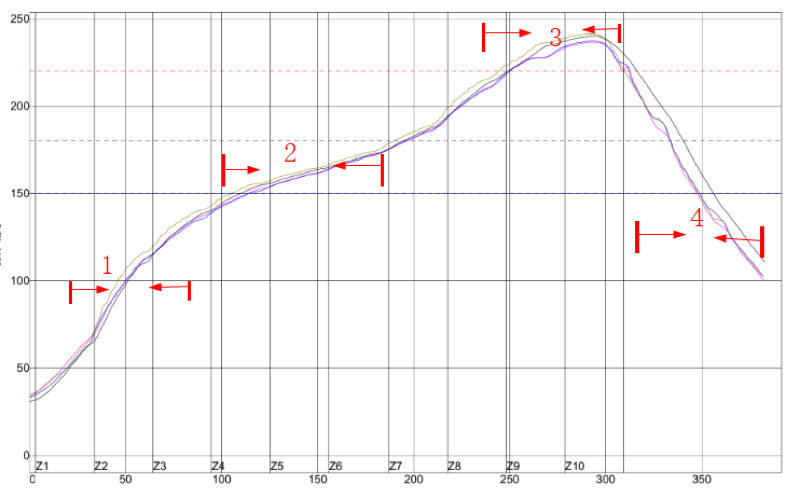
1.The Preheating Zone
The preheating zone serves to evaporate the lower melting solvent present in the solder paste. Key constituents of the flux within the solder paste encompass resin, active agent, viscosity enhancer, and solvent. The solvent primarily acts as a carrier for the resin while also ensuring adequate storage time for the solder paste. It is imperative for the preheating zone to evaporate the solvent while carefully managing temperature escalation. Excessive heating can induce thermal stress on the components, potentially leading to component damage or diminished performance/lifespan. Additionally, excessively rapid heating may cause the solder paste to collapse, risking short circuits, particularly evident in solder pastes with high flux content.
2.The Constant Zone
The constant temperature zone is primarily governed by the specifications provided by the solder paste supplier and the heat capacity of the PCB. This phase serves two key purposes.
Firstly, it aims to establish a uniform temperature across the entire PCB board. This aids in minimizing thermal stress during reflow and mitigates soldering defects such as component lifts, particularly in larger volume productions. Additionally, this stage initiates active flux reaction within the solder paste, enhancing the wettability and surface energy of the soldering surface. This ensures effective wetting of the molten solder on the surface, a critical aspect of the soldering process. Therefore, precise control of soaking time and temperature is essential to ensure thorough cleaning of the soldering surface by the flux while preventing its complete consumption before reaching reflow. Retaining sufficient flux during reflow is imperative as it facilitates the solder wetting process and prevents reoxidation of the soldered surface.
Firstly, it aims to establish a uniform temperature across the entire PCB board. This aids in minimizing thermal stress during reflow and mitigates soldering defects such as component lifts, particularly in larger volume productions. Additionally, this stage initiates active flux reaction within the solder paste, enhancing the wettability and surface energy of the soldering surface. This ensures effective wetting of the molten solder on the surface, a critical aspect of the soldering process. Therefore, precise control of soaking time and temperature is essential to ensure thorough cleaning of the soldering surface by the flux while preventing its complete consumption before reaching reflow. Retaining sufficient flux during reflow is imperative as it facilitates the solder wetting process and prevents reoxidation of the soldered surface.
3.The High-Temperature Zone
The high-temperature zone is where the complete melting and wetting reaction occur, initiating the formation of the inter-metallic compound layer. Once the maximum temperature (typically above 217°C) is attained, the temperature begins to decrease, eventually falling below the return line, leading to solder solidification. It's crucial to meticulously regulate this stage to avoid subjecting components to thermal shock due to abrupt temperature changes. The maximum temperature in the reflow zone is determined by the temperature tolerance of temperature-sensitive components on the PCB. The duration spent in the high-temperature zone should be minimized to ensure adequate soldering of components while preventing excessive thickening of the inter-metallic compound layer. Generally, the optimal duration in this zone ranges from 30 to 60 seconds. Prolonged exposure or excessively high temperatures can compromise the long-term reliability of the solder joint.
4.The Cooling Zone
The significance of cooling zones within the overall reflow soldering process is often underestimated. An effective cooling process is pivotal in achieving desirable weld outcomes. High-quality solder joints are characterized by their bright and smooth appearance. However, inadequate management of the cooling phase can lead to various issues, including component lift, darkened solder joints, surface unevenness in solder joints, and excessive thickening of the intermetallic compound layer. Hence, it's imperative for reflow soldering to incorporate a well-balanced cooling curve that neither progresses too swiftly nor too slowly. Excessive slowness in cooling can result in the aforementioned problems due to insufficient cooling, while overly rapid cooling may subject components to thermal shock. Finding the right balance is crucial for optimal solder joint quality.
Components of the Temperature Curve
A comprehensive understanding of the temperature curve necessitates insight into its constituent elements:
Temperature Profile: The curve's trajectory, characterized by ramp-up rates, peak temperatures, and dwell times, dictates the soldering kinetics and final joint morphology.
Thermal Profile Controller: This critical component regulates the heating and cooling rates, ensuring adherence to the desired temperature curve and minimizing process variations.
Flux Activation: The temperature curve activates the flux within the solder paste, facilitating the removal of oxides and promoting solder wetting for strong intermetallic bonding.
Intermetallic Compound Formation: The high-temperature zone fosters the formation of intermetallic compounds, essential for enhancing solder joint reliability and mechanical strength.
Temperature Profile: The curve's trajectory, characterized by ramp-up rates, peak temperatures, and dwell times, dictates the soldering kinetics and final joint morphology.
Thermal Profile Controller: This critical component regulates the heating and cooling rates, ensuring adherence to the desired temperature curve and minimizing process variations.
Flux Activation: The temperature curve activates the flux within the solder paste, facilitating the removal of oxides and promoting solder wetting for strong intermetallic bonding.
Intermetallic Compound Formation: The high-temperature zone fosters the formation of intermetallic compounds, essential for enhancing solder joint reliability and mechanical strength.
Mastering Controlled Heating
Achieving mastery over the SMT solder reflow temperature curve demands precision, finesse, and technological prowess:
Optimized Process Parameters: Fine-tuning ramp rates, peak temperatures, and dwell times in alignment with solder paste specifications and component requirements is essential for consistent solder joint quality.
Thermal Management: Effective thermal profiling and heat transfer mechanisms prevent thermal gradients, component overheating, and solder defects, ensuring uniform heating across the assembly.
Real-Time Monitoring: Continuous monitoring of temperature profiles and solder joint characteristics enables prompt adjustments, preempting potential defects and optimizing process efficiency.
Innovative Technologies: Leveraging advanced reflow equipment, such as infrared and vapor phase systems, enhances temperature control and process stability, elevating soldering precision to new heights.
Optimized Process Parameters: Fine-tuning ramp rates, peak temperatures, and dwell times in alignment with solder paste specifications and component requirements is essential for consistent solder joint quality.
Thermal Management: Effective thermal profiling and heat transfer mechanisms prevent thermal gradients, component overheating, and solder defects, ensuring uniform heating across the assembly.
Real-Time Monitoring: Continuous monitoring of temperature profiles and solder joint characteristics enables prompt adjustments, preempting potential defects and optimizing process efficiency.
Innovative Technologies: Leveraging advanced reflow equipment, such as infrared and vapor phase systems, enhances temperature control and process stability, elevating soldering precision to new heights.
Conclusion
In the realm of SMT assembly, the solder reflow temperature curve serves as both a science and an art form. Its mastery is indispensable for achieving robust solder joints, optimal electronic performance, and the seamless integration of modern technologies. By understanding the intricacies of the temperature curve and embracing advanced methodologies, manufacturers can embark on a journey towards excellence, where precision soldering meets the demands of ever-evolving electronic applications.
Tell us about your project below and we would be happy to help with your PCB manufacturing processes and goals!
Tell us about your project below and we would be happy to help with your PCB manufacturing processes and goals!
Originally Posted On: https://www.hvttec.com/smt-solder-reflow-temperature-curve.html
Comments