To expand your news reach, consider advertising with our media partner, Patch Media, at https://heypapipromotionsmedia.town.news/. Patch is a nationwide news network comprising over 1,000 hyperlocal websites dedicated to community news across the United States. For press release distribution services, please call or visit https://heypapipromotions.com/advertise.
Sheet metal process or sheet metal fabrication includes: folding, shearing, punching, welding, riveting, splicing and other processes. In general, the process of forming a sheet by hand or mechanical is called sheet metal processing. Sheet metal processing is to cut and bend metal materials into various shapes and their thicknesses can vary significantly. According to the materials, sheet metal fabrication can be divided into several types, including aluminum sheet metal fabrication, stainless steel fabrication and brass fabrication.
Sheet metal process:
1. Drawing design:
In general, the customer provide drawings or samples, then our engineers perform the measurement, design, and development, and form the machining decomposition map and assembly drawing to the production department for processing.
2. Laser processing:
It has a large laser cutting machine, it can be cut by laser cutting such as carbon steel, stainless steel, etc material. After the workpiece is processed, the section is neat, smooth and beautiful, and the size is accurate. It has advantages for the workpiece with arc. CNC stamping can not replace the processing method.
3. CNC stamping:
With imported turret CNC punching machine, CNC punching is mainly for the thickness of product processing materials, generally suitable for materials below 2.5mm. Sheet metal processing workpieces have more holes or need to open special molds to process the workpiece. CNC punching has a certain cost advantage.
4. Bend:
After the workpiece is cut, if most of them need to be bent and formed, the CNC bending machine not only has a fast speed, but also the workpiece is processed more accurately.
5. Welding molding:
The workpiece needs to be assembled and formed after cutting the material, and the assembly method is various. Some are directly formed by non-welding processes such as screws and riveting. Generally, the mechanical casing is made of welding, and the company adopts argon arc welding, bump welding, carbon dioxide welding, etc., we will polished them after welding, so that the workpiece is relatively firm and beautiful.
6. Electrostatic powder spray:
Electrostatic powder spraying is mainly for carbon steel workpieces. In the process, oil removal and derusting, surface cleaning, phosphating, electrostatic powder spraying and high temperature baking are generally carried out. After processing, the surface of the workpiece is beautiful, it will not rust within a few years, and the cost is low.
Liquid paint: This process differs from electrostatic powder spray. It is mainly used for large workpieces. It is convenient and low-cost to use liquid paint when it cannot be handled. The liquid paint is divided into two steps, and the primer is applied to the paint after the workpiece is processed.
7. Packaging and shipping:
100% inspection before packaging and inspection data.
Advantages of Sheet Metal
Sheet metal has the characteristics of light weight, high strength, electrical conductivity (can be used for electromagnetic shielding), low cost, large-scale mass production performance, etc. It has been widely used in the fields of electronics, telecommunications, automotive industry, medical equipment and so on. For example, in computer cases, mobile phones, and MP3s, sheet metal is an essential part.
Sheet Metal Applicaitons
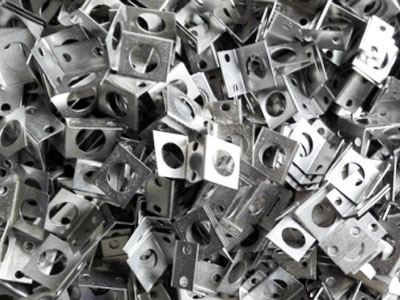
Electronic and electrical parts
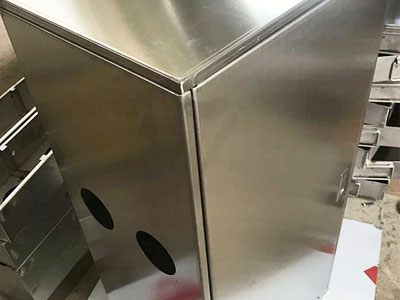
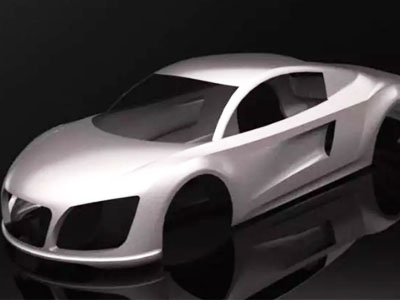
Car shell

Auto parts
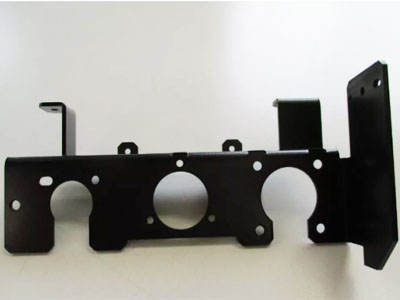
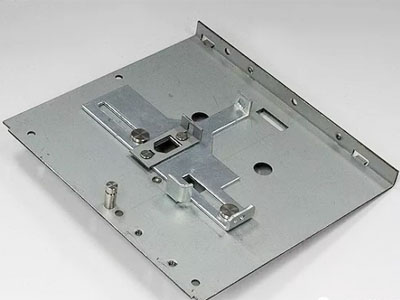
Comments