To expand your news reach, consider advertising with our media partner, Patch Media, at https://heypapipromotionsmedia.town.news/. Patch is a nationwide news network comprising over 1,000 hyperlocal websites dedicated to community news across the United States. For press release distribution services, please call or visit https://heypapipromotions.com/advertise.
Soldering is a cornerstone of electronics manufacturing, especially when connecting metals in printed circuit board (PCB) assembly, where flux is vital for achieving solder joint reliability. This reliability ensures that joints withstand daily wear, environmental stress, and mechanical strain without cracking or failing. This guide explores the types of flux available, their benefits and limitations, and flux removal methods, all tailored to enhance solder joint reliability in electronic products.
Flux facilitates soldering and desoldering by removing oxide layers, improving solder wetting, and ensuring even flow—key factors in achieving solder joint reliability. In electronic soldering, flux promotes robust connections between components, critical for solder joint reliability. Soldering uses a molten alloy, or solder, to bond metal surfaces, but impurities, oxides, and contaminants can undermine solder joint reliability. Flux counters these issues by cleaning surfaces, enabling strong, dependable metallurgical bonds essential for long-term solder joint reliability.
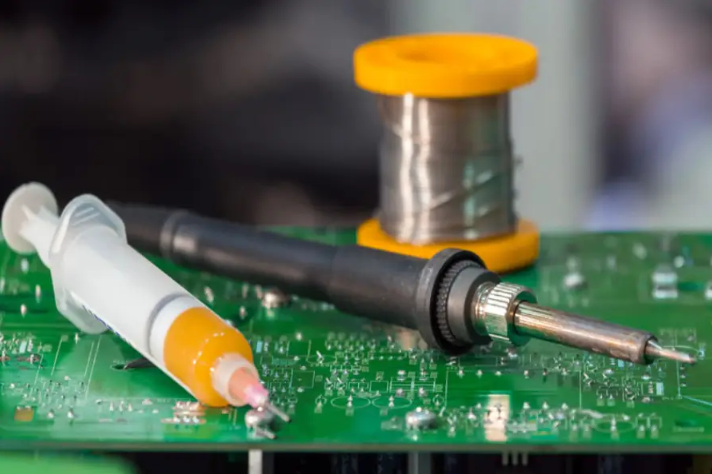
Understanding Flux and Its Role in Solder Joint Reliability
Flux is a compound that prepares metal surfaces for soldering by removing oxides, promoting wetting, and enhancing solder flow—all crucial for solder joint reliability. Available as paste, liquid, or within solder wire cores, flux contains active agents like rosin or organic acids that react with surface oxides. When heated, flux activates, clearing oxides to prevent interference, directly supporting solder joint reliability. By reducing solder surface tension, flux ensures uniform spreading, forming joints that bolster solder joint reliability.
Moreover, flux forms a protective barrier during soldering, preventing oxide reformation and preserving solder joint reliability by shielding cleaned surfaces from atmospheric oxygen. This protection is vital for maintaining clean, consistent joints that ensure solder joint reliability in electronic applications. For advanced soldering processes, equipment like the Vacuum Soldering System KD-V200HT can further enhance this process by providing a controlled vacuum environment, minimizing oxidation and improving solder joint reliability. The KD-V200HT is particularly effective for high-precision applications where maintaining a pristine soldering environment is critical.
Types of Flux and Their Impact on Solder Joint Reliability
Different flux types address varying soldering needs, each influencing solder joint reliability based on their formulation and activity level. Some target specific metals like copper, while others offer versatility, with activity ranging from mild to highly active depending on oxidation levels affecting solder joint reliability.
IPC J-Standard Flux Classification for Solder Joint Reliability
- The IPC J-Standard classifies flux by composition and activity, a system critical for ensuring solder joint reliability in modern electronics. Categories include Rosin (RO), Organic (OR), Inorganic (IN), and Resin/Synthetic Resin (RE), with activity levels of Low (L, <0.5% halide), Moderate (M, 0-2% halide), or High (H, >2% halide). Halide content (Cl- or Br-) splits them into 0 (no halide) or 1 (some halide). For instance, ROL0 is a low-activity, halide-free rosin flux ideal for basic solder joint reliability, while ROM1 (e.g., RMA with 0.5-2% halide) offers moderate activity for more challenging solder joint reliability needs.
Rosin (R-Type) Flux and Solder Joint Reliability
- Rosin flux, derived from pine tar resin, is a traditional choice for soldering, leveraging natural acids like abietic acid to enhance solder joint reliability. In its basic R-type form, rosin dissolved in solvents like isopropyl alcohol lacks activators, suiting simple tasks where solder joint reliability is less demanding. For tougher oxides—common with lead-free alloys at higher temperatures—activators create Rosin Mildly Activated (RMA) or Rosin Activated (RA) fluxes. These include organic acids, halides, or salts, boosting solder joint reliability by tackling heavy oxide layers.
- However, activated rosin fluxes can leave corrosive residues like chloride ions, threatening solder joint reliability if not removed post-soldering. These tacky remnants may attract conductive dust, risking short circuits and undermining solder joint reliability. With lead-free soldering’s rise, higher temperatures necessitate active fluxes, making thorough cleaning critical for sustained solder joint reliability. For lead-free soldering, the Inline Void-Free Reflow Oven for Diode KD-V10S HVT can be a game-changer. The KD-V10S HVT reduces voids in solder joints, directly contributing to improved solder joint reliability by ensuring consistent bonding at elevated temperatures.
No-Clean Flux and Solder Joint Reliability
- No-clean fluxes, using rosin or synthetic resins, aim to simplify processes while supporting solder joint reliability. Rosin-based versions have lower rosin content than R-type fluxes, while synthetic options mimic rosin’s properties. Though some include mild activators, residues can still affect solder joint reliability if corrosive.
- Designed to minimize cleanup, no-clean fluxes leave less residue than R-type fluxes, typically insufficient to disrupt solder joint reliability or cause corrosion over time. Yet, sticky residues may attract dust, impacting aesthetics or solder joint reliability in sensitive applications. For conformal coating, even minimal residue must be removed to ensure coating adhesion and preserve solder joint reliability. With lead-free alloys requiring active fluxes, cleanup may still be needed, potentially offsetting no-clean benefits for solder joint reliability. In such cases, using the Vacuum Reflow Soldering Oven KD_V10N HVT can help. The KD_V10N HVT offers precise temperature control in a vacuum environment, reducing residue issues and enhancing solder joint reliability for lead-free soldering applications.
Water-Soluble Flux and Solder Joint Reliability
- Water-soluble fluxes, often resin-based, require water rinsing to remove residues, directly impacting solder joint reliability. Some are water-based, reducing VOC emissions—a plus for eco-conscious manufacturers aiming for solder joint reliability under strict regulations. Activators like organic acids or halides, while effective, are corrosive, necessitating removal to safeguard solder joint reliability over time.
Flux Formats and Their Contribution to Solder Joint Reliability
Flux comes in various formats—liquid, tacky, flux-cored solder, and solder paste—each enhancing solder joint reliability based on application needs and soldering methods.
- Liquid Flux: Applied via bottles, syringes, or pens, liquid flux cleans surfaces before soldering, improving flow and ensuring solder joint reliability. It’s vital in wave soldering, where precise application via spray or foam supports consistent solder joint reliability.
- Tacky Flux: With a gel-like consistency, tacky flux adheres to surfaces, ideal for vertical joints where maintaining position enhances solder joint reliability.
- Flux-Cored Solder: Combining solder and flux in a wire core, this format cleans surfaces as it melts, streamlining processes and bolstering solder joint reliability.
- Flux in Solder Paste: Used in surface-mount technology (SMT), solder paste integrates flux with alloy particles, securing components and promoting solder joint reliability during reflow. For SMT applications, the Inline Vacuum Soldering Systems KD_V400 can optimize the reflow process. The KD_V400 ensures uniform heating and a controlled vacuum environment, which minimizes defects and improves solder joint reliability in SMT soldering.
Ensuring Solder Joint Reliability Through Flux Selection and Advanced Equipment
Flux is indispensable for solder joint reliability, removing oxides, enhancing wetting, and preventing re-oxidation. These functions create robust joints critical for electronic performance. Choosing the right flux—rosin, no-clean, or water-soluble—optimizes solder joint reliability by matching the soldering task’s demands. For instance, RMA flux suits lead-free soldering where oxide removal is key to solder joint reliability, while no-clean flux supports quick assembly with minimal cleanup, assuming residues don’t compromise solder joint reliability.
Advanced equipment can further enhance solder joint reliability. For power module applications requiring precise bonding, the Inline 4-Chambers Vacuum Soldering Oven with Formic Acid KD-V400L provides a controlled environment that reduces defects. The KD-V400L uses formic acid to further clean surfaces during soldering, ensuring solder joint reliability by minimizing oxidation and supporting consistent joint quality in high-power applications.
Post-soldering flux removal is equally critical for solder joint reliability. Corrosive residues from activated fluxes must be cleaned to prevent long-term degradation, ensuring solder joint reliability in harsh environments. Even no-clean fluxes may require removal for aesthetic or coating purposes, reinforcing solder joint reliability in high-stakes applications.
Conclusion
Flux underpins solder joint reliability in electronic soldering, enabling clean, strong connections that withstand operational stresses. By selecting appropriate flux types and formats—whether rosin for traditional needs, no-clean for efficiency, or water-soluble for eco-friendliness—and leveraging advanced equipment like the Vacuum Soldering System KD-V200HT, Inline Void-Free Reflow Oven for Diode KD-V10S HVT, Vacuum Reflow Soldering Oven KD_V10N HVT, Inline Vacuum Soldering Systems KD_V400, and Inline 4-Chambers Vacuum Soldering Oven with Formic Acid KD-V400L, manufacturers can enhance solder joint reliability across PCB assembly and beyond. Proper flux management, including residue removal where necessary, ensures that solder joint reliability remains uncompromised, delivering durable, high-performing electronic products in 2025 and beyond.
Comments