Sheet metal is known for its exceptional versatility and widespread use across various industries. Among its many variations, perforated sheets play a niche yet crucial role in specific applications.
In this guide, we aim to provide you with comprehensive insights into perforated sheets—exploring their common uses, unique characteristics, and the manufacturing process behind them.
In this guide, we aim to provide you with comprehensive insights into perforated sheets—exploring their common uses, unique characteristics, and the manufacturing process behind them.
What Is Perforated Sheet and How Does It Work?
Sheet metal is a thin, flat material widely used in various industries, from automotive to electronics. Perforated sheet metal, on the other hand, is distinguished by its numerous punched holes arranged in regular patterns.
These perforated sheets can feature different hole shapes such as squares, rectangles, and oblongs, but circular holes in a staggered pattern are the most common. This design choice enhances manufacturing efficiency, improves aesthetics, and strengthens the sheet.
The process of creating perforated sheets involves using automated punching machines, either CNC-controlled or mechanically operated, to precisely punch holes into regular sheet metal.
These perforated sheets can feature different hole shapes such as squares, rectangles, and oblongs, but circular holes in a staggered pattern are the most common. This design choice enhances manufacturing efficiency, improves aesthetics, and strengthens the sheet.
The process of creating perforated sheets involves using automated punching machines, either CNC-controlled or mechanically operated, to precisely punch holes into regular sheet metal.
The Process of Making Perforated Sheet Metal
Perforated sheet metal typically begins as a coil of sheet metal with a specific gauge thickness. Gauge sizes vary by country, where a higher gauge number indicates thinner sheet metal. Once the gauge is selected, various manufacturing methods can be used to fabricate perforated sheet metal.
The top three modern manufacturing processes for perforated sheet metal include rotary-pinned perforation, punch press, and laser perforation.
Rotary-Pinned Perforation
Rotary-pinned perforation is the most common and efficient method for producing high-quality perforated sheet metal. This process utilizes large cylinders equipped with sharp needles on their surface. The cylinders rotate at high speeds, sometimes heated to temperatures above 400 degrees Celsius, to punch holes into the passing sheet metal. This heat treatment strengthens the perforations, improving their load resistance and overall strength. Due to their high speed, rotary-pinned perforation is cost-effective and capable of producing large quantities of identical holes rapidly.
Punch Press
A punch press uses a ram to compress sheet metal against a fixed die, shaping and cutting holes in the metal. Punch presses can be manually operated or computer numerically controlled (CNC). CNC-controlled punch presses automate production, improving efficiency and precision.
The top three modern manufacturing processes for perforated sheet metal include rotary-pinned perforation, punch press, and laser perforation.
Rotary-Pinned Perforation
Rotary-pinned perforation is the most common and efficient method for producing high-quality perforated sheet metal. This process utilizes large cylinders equipped with sharp needles on their surface. The cylinders rotate at high speeds, sometimes heated to temperatures above 400 degrees Celsius, to punch holes into the passing sheet metal. This heat treatment strengthens the perforations, improving their load resistance and overall strength. Due to their high speed, rotary-pinned perforation is cost-effective and capable of producing large quantities of identical holes rapidly.
Punch Press
A punch press uses a ram to compress sheet metal against a fixed die, shaping and cutting holes in the metal. Punch presses can be manually operated or computer numerically controlled (CNC). CNC-controlled punch presses automate production, improving efficiency and precision.
- Wide Punch Press: Features multiple rams aligned in rows that descend simultaneously to punch rows of holes in the sheet metal.
- XY-Axis Machine: Utilizes a single die or a group of punching rams to create holes in intricate patterns and non-repetitive designs. The sheet metal is typically held in place as the machine moves to punch holes, leaving non-perforated areas that enhance the finished appearance.
Laser Perforation
Laser perforation employs precision beams to burn through the sheet metal, creating precise and intricate patterns of holes. This method offers high accuracy and flexibility but can be time-consuming and expensive for large-scale production.
Laser perforation employs precision beams to burn through the sheet metal, creating precise and intricate patterns of holes. This method offers high accuracy and flexibility but can be time-consuming and expensive for large-scale production.
What Type of Sheet Material Can Be Perforated?
Perforated sheets can be made from nearly any sheet metal material, although steel and aluminum are the most frequently used. These sheets are available in a variety of thicknesses, ranging from 0.019 inches to 0.250 inches thick.
Standard sheet sizes are commonly used for perforated sheets, but at Huijin Metal, we offer the flexibility to cut sheets to any size you need, ensuring they meet your specific requirements.
Standard sheet sizes are commonly used for perforated sheets, but at Huijin Metal, we offer the flexibility to cut sheets to any size you need, ensuring they meet your specific requirements.
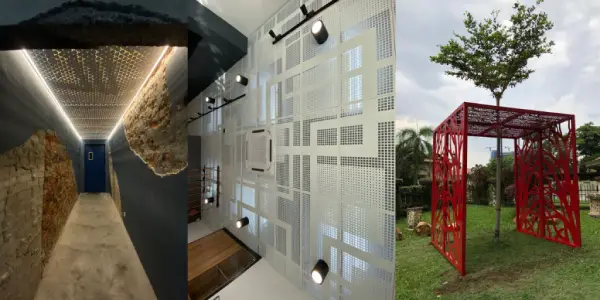
Applications of Perforated Sheets
Perforated sheets serve numerous applications across various industries, and the following list provides just a glimpse of their diverse uses!
Acoustic Applications
- Acoustic Panels: Used in sound-critical environments like recording studios to dampen, reflect, or dissipate sound waves.
- Acoustic Equipment Framework: Enhances sound system performance while providing structural support and encasement for electronic components.
Automotive Uses
- Exhaust Baffling: Installed inside mufflers to dissipate sound waves and contain wadding without obstructing gas flow.
- Speaker Grilles: Typically made from thin aluminum sheets.
Construction and Architectural Uses
- Building Facades: Aluminum or painted steel perforated sheets used as design features and for acoustic damping on modern building exteriors.
- Aggregate Filters: Heavy perforated sheets utilized in construction site landscaping for filtering and grading bulk materials.
Water & Waste Management Filtration
- Filters and Screens: Ideal for creating filters that allow water and small particles to pass through while blocking larger debris.
- Staged Filtration: Customizable hole sizes enable the creation of multi-stage filtration systems that progressively filter smaller particles.
Bespoke Fabrications
- Cooling and Ventilation Panels: Used on electrical equipment to provide airflow for cooling while ensuring safety from contact.
- Store Displays: Creative designers use perforated sheets in shop displays to add visual interest and break up the design.
Benefits of Utilizing Perforated Sheets
Cost Efficiency
While mesh screens can be customized with laser cutting, this process tends to be expensive. Perforated sheets, on the other hand, offer a cost-effective solution for filtration, airflow, and various other applications mentioned earlier, available in ready-to-use configurations.
Versatility in Fabrication
Perforated sheets can be easily tailored to bespoke shapes and sizes using tools like laser cutters, guillotines, and press brakes, just like regular sheet metal. For more details on these fabrication methods, refer to our comprehensive guide here.
Wide Range of Sizes for Every Need
Available in various thicknesses and materials, perforated sheets cater to both light-duty and heavy-duty applications. Whether used as painted architectural features or corrosion-resistant filtration systems, perforated sheets offer versatility. Hole sizes range from 0.063 inches to 2.0 inches, ensuring there's a suitable type for your specific requirements.
At Huijin Metal, we stock perforated sheets in mild steel and aluminum, offering a wide selection of thicknesses. Explore our full range of products to find the perfect solution for your project needs.
While mesh screens can be customized with laser cutting, this process tends to be expensive. Perforated sheets, on the other hand, offer a cost-effective solution for filtration, airflow, and various other applications mentioned earlier, available in ready-to-use configurations.
Versatility in Fabrication
Perforated sheets can be easily tailored to bespoke shapes and sizes using tools like laser cutters, guillotines, and press brakes, just like regular sheet metal. For more details on these fabrication methods, refer to our comprehensive guide here.
Wide Range of Sizes for Every Need
Available in various thicknesses and materials, perforated sheets cater to both light-duty and heavy-duty applications. Whether used as painted architectural features or corrosion-resistant filtration systems, perforated sheets offer versatility. Hole sizes range from 0.063 inches to 2.0 inches, ensuring there's a suitable type for your specific requirements.
At Huijin Metal, we stock perforated sheets in mild steel and aluminum, offering a wide selection of thicknesses. Explore our full range of products to find the perfect solution for your project needs.
What Can I Do to Customize My Project?
Modern perforated sheet metal offers incredible versatility to meet diverse design requirements. If you're considering perforated sheet metal for your upcoming project, here are the customization options we provide:
- Raw Materials: Perforated sheet metal can be crafted from various materials such as aluminum, zinc alloys, steel (including galvanized and stainless steel), and copper. For outdoor applications requiring corrosion resistance, materials like zinc, galvanized steel, or aluminum are ideal. Copper and stainless steel are often chosen for their aesthetic appeal in indoor settings.
- Designs and Patterns: Our computer-controlled laser cutting system ensures precise cutting of intricate shapes and patterns, meeting the most demanding design specifications.
- Sheet Shapes: Sheet metal's flexibility allows for creating custom shapes like waves, curves, or scallops. We employ cutting-edge techniques such as cutting, welding, and bending to achieve your desired design.
- Finishing: The finishing process enhances the appearance and durability of perforated sheet metal. Options include powder coating, galvanizing, and anodizing, which not only add brightness, color, and texture but also improve resistance to wear and corrosion.
Comments