What Is Moisture Wicking Polyester Fabric?
Moisture wicking polyester fabric refers to a type of technical textile engineered to draw sweat away from the body and transfer it to the outer surface of the fabric, where it evaporates quickly. Unlike traditional cotton or wool, polyester doesn't absorb moisture into its fibers but instead relies on capillary action to transport liquid. When treated or structured correctly, polyester becomes an excellent material for high-performance garments—especially in activewear and modern men's dress pants.
This fabric is widely used in various industries, including sportswear, uniforms, and now increasingly in business casual and office attire. Its functionality makes it a go-to option for brands aiming to merge comfort with style.
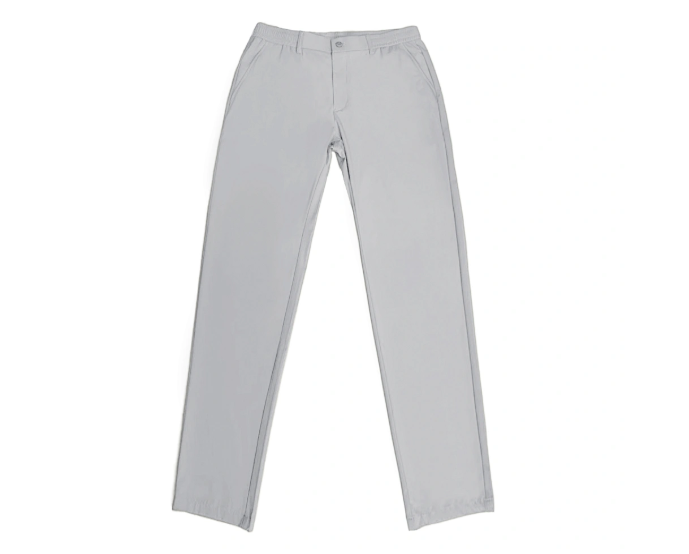
Why Consider Moisture Wicking Polyester Fabric for Men's Dress Pants?
In today's fast-paced world, men need trousers that can keep up with both professional and physical demands. Whether commuting in humid weather, moving between meetings, or simply seeking all-day comfort, moisture wicking polyester fabric provides a practical solution.
Key Advantages:
- Sweat Management: Keeps you dry throughout the day.
- Breathability: Enhances airflow compared to traditional blends.
- Durability: Polyester holds up well against repeated washing and wear.
- Wrinkle Resistance: Ideal for maintaining a clean, polished look.
- Lightweight Feel: Comfortable even in warmer climates or active settings.
These benefits make it especially ideal for garments like Men's Elastic Waist Dress Pants, which are designed for both comfort and functionality.
How Does Moisture Wicking Technology Work?
The science behind moisture wicking polyester fabric is relatively straightforward. The synthetic fibers are designed with a cross-section shape or a chemical finish that allows moisture to move rapidly across the fabric’s surface. The goal is not to absorb water but to spread it out across a larger area to enable faster evaporation.
This quick-drying effect reduces skin irritation, keeps odor at bay, and provides a more hygienic wearing experience.
Is Moisture Wicking Polyester Fabric Breathable?
One common misconception is that synthetic fabrics like polyester are less breathable than natural fibers. While that may be true for untreated polyester, moisture wicking polyester fabric is specifically engineered for airflow and breathability.
In many cases, micro-perforations or mesh structures are added to increase ventilation. Some advanced types even combine recycled polyester with elastane or bamboo-derived fibers for extra breathability and stretch, enhancing their performance in dress pants designed for movement.
Does Moisture Wicking Polyester Fabric Feel Comfortable?
Absolutely—when designed properly. In premium dress pants, such as RE&X’s modern performance collections, moisture wicking polyester fabric is often blended with spandex or rayon to achieve a soft, smooth finish that feels great against the skin.
Unlike older polyester fabrics that felt stiff or plasticky, new-generation moisture-wicking textiles are engineered for comfort and elegance. This makes them perfect for modern Men's Elastic Waist Dress Pants, where comfort and mobility are top priorities.
Are Moisture Wicking Polyester Dress Pants Formal Enough?
Traditionally, dress pants were made from wool, cotton twill, or blends. However, modern tailoring techniques and fabric innovations have changed that. Today’s moisture wicking polyester fabric can be woven into fine textures that resemble classic suiting materials while offering additional benefits like:
- Less creasing during travel
- Easier maintenance
- All-day freshness
- UV protection
As long as the cut, fit, and design adhere to dress codes, polyester dress pants can be just as formal—and often more practical—than their natural fiber counterparts.
How Does Moisture Wicking Polyester Fabric Perform in Hot or Humid Weather?
One of the standout features of moisture wicking polyester fabric is its ability to manage body heat. In hot or humid climates, where traditional wool pants may feel heavy and damp, polyester-based fabrics excel by:
- Moving moisture away from the skin
- Drying quickly
- Maintaining shape despite sweat
- Preventing bacterial growth and odor
These properties are especially useful for businessmen or commuters who face varying indoor and outdoor temperatures.
Is It Sustainable to Use Moisture Wicking Polyester Fabric?
While polyester is a synthetic material derived from petroleum, many manufacturers are now moving toward eco-friendly alternatives. Recycled polyester (rPET), derived from plastic bottles and industrial waste, retains all the benefits of moisture-wicking properties while reducing environmental impact.
Brands committed to sustainability—like RE&X—are incorporating such materials into their collections, ensuring that modern style doesn’t come at the planet’s expense.
What Are the Downsides of Moisture Wicking Polyester Fabric?
While moisture wicking polyester fabric offers numerous advantages, it's not without its challenges:
- Heat Retention: Poorly constructed versions may feel warm in extreme heat.
- Static Build-Up: Especially in dry conditions, though this can be managed with fabric treatments.
- Environmental Concerns: Virgin polyester is not biodegradable, highlighting the importance of choosing recycled options.
Understanding these limitations can help consumers make informed choices and identify higher-quality garments.
How to Care for Moisture Wicking Polyester Dress Pants?
Proper care ensures your pants retain their moisture wicking ability and look sharp for years. Tips include:
- Machine wash cold: Avoid hot water to preserve the fibers.
- Use mild detergent: Harsh chemicals can degrade fabric treatments.
- Avoid fabric softeners: They can block the fabric’s capillaries and reduce wicking ability.
- Tumble dry low or air dry: Prevent shrinkage and heat damage.
Moisture wicking polyester fabric is low-maintenance, making it perfect for men seeking hassle-free yet stylish trousers.
Who Should Wear Moisture Wicking Dress Pants?
These trousers are perfect for:
- Office professionals: Stay dry and sharp all day long.
- Frequent travelers: Lightweight, wrinkle-resistant, and easy to pack.
- Active individuals: For those who walk or bike to work.
- Anyone in warm climates: Keep cool and comfortable during hot months.
They’re especially popular in performance categories like Men's Elastic Waist Dress Pants, which combine comfort, fit, and stretch with refined aesthetics.
What Are the Best Moisture Wicking Polyester Fabric Blends?
Some common and effective blends include:
- Polyester + Spandex: For stretch and flexibility
- Polyester + Rayon: For softness and drape
- Polyester + Wool: For a formal look with added functionality
- Recycled Polyester Blends: For sustainability without performance loss
These blends are carefully selected to achieve the right balance of elegance and performance in men’s dress pants.
Conclusion: Should You Choose Moisture Wicking Polyester Fabric for Dress Pants?
If you're looking for modern, functional, and comfortable trousers that keep up with your lifestyle, moisture wicking polyester fabric is an excellent option. Whether it’s to manage sweat during a long commute, stay crisp through a business meeting, or enjoy easy maintenance, these fabrics deliver where it counts.
And when integrated into smart designs like Men's Elastic Waist Dress Pants, they offer the ultimate fusion of style, practicality, and comfort.
While no fabric is perfect for every situation, moisture wicking polyester fabric offers a compelling case for the future of men’s dress wear.