Air separation units (ASUs) are essential for producing industrial gases such as oxygen, nitrogen, and argon, which are vital across sectors like healthcare, metallurgy, chemicals, and energy. These units employ advanced technologies like cryogenic distillation and pressure swing adsorption (PSA) to separate air into its constituent gases. As demand for high-purity gases grows, air separation unit suppliers play a pivotal role in delivering innovative and efficient solutions. This article highlights some of the most prominent suppliers in the industry, their technologies, and their contributions to global markets.
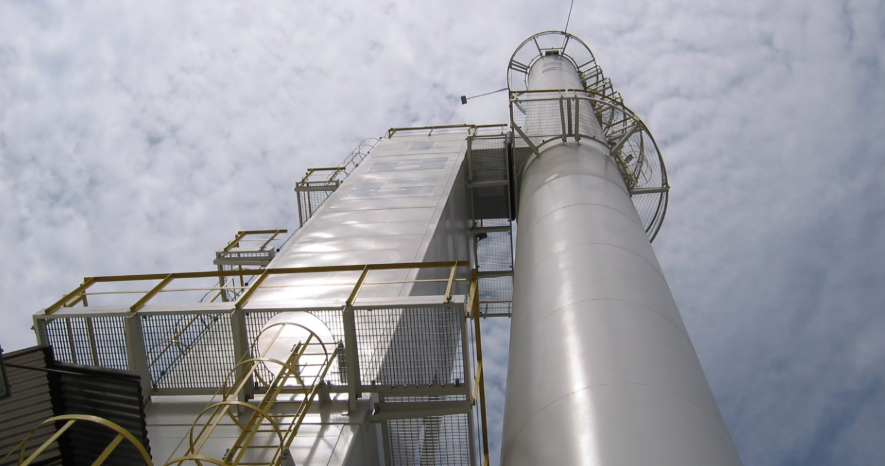
What Are Air Separation Units?
Air separation units are sophisticated systems designed to extract gases from atmospheric air. The primary methods include:
- Cryogenic Air Separation: This process cools air to extremely low temperatures to liquefy and separate gases based on their boiling points. It is ideal for large-scale production of high-purity oxygen, nitrogen, and argon.
- Pressure Swing Adsorption (PSA): PSA uses adsorbent materials to selectively capture gases, making it suitable for smaller-scale or on-site gas generation.
- Membrane Separation: This method uses selective membranes to separate gases, often used for nitrogen production in less demanding applications.
Air separation unit suppliers specialize in designing and manufacturing these systems, tailoring them to industries like steel production, medical oxygen supply, and chemical processing.
Leading Air Separation Unit Suppliers
The global market for air separation units is dominated by a few key players known for their technological expertise and extensive project experience. Below, we explore some of the top air separation unit suppliers shaping the industry.
Linde plc
Linde is one of the world’s largest industrial gas companies and a leading air separation unit supplier. Headquartered in Germany, Linde offers a comprehensive range of ASUs, including cryogenic plants and PSA systems. Their cryogenic air separation units are renowned for energy efficiency and scalability, serving industries like steelmaking and healthcare.
Linde’s global presence includes projects in over 100 countries, such as large-scale oxygen plants for chemical manufacturing in Asia and nitrogen generators for oil and gas operations in the Middle East. Their focus on sustainability, including carbon capture integration, sets them apart as an innovative air separation unit supplier.
Air Liquide
Based in France, Air Liquide is another titan among air separation unit suppliers. With over a century of experience, the company provides customized ASU solutions for industries ranging from electronics to aerospace. Air Liquide’s cryogenic ASUs are designed for high reliability, while their PSA and membrane systems cater to on-site gas needs.
Air Liquide has a strong footprint in emerging markets, with notable projects like liquid nitrogen plants in India and oxygen supply systems for hospitals in South America. Their commitment to digitalization, including smart monitoring for ASUs, enhances operational efficiency, making them a preferred air separation unit supplier.
Air Products and Chemicals, Inc.
Air Products, headquartered in the United States, is a global leader in industrial gases and a top air separation unit supplier. The company specializes in large-scale cryogenic ASUs, delivering high-purity gases for refining, petrochemicals, and LNG production. Their proprietary technologies optimize energy use and reduce emissions.
Air Products has executed landmark projects, such as supplying oxygen for gasification plants in Saudi Arabia and nitrogen for electronics manufacturing in South Korea. Their modular PSA systems are also popular for on-site gas generation, cementing their reputation as a versatile air separation unit supplier.
Praxair (Now Part of Linde)
Praxair, now integrated into Linde, was historically a major player in the ASU market. Before the merger, Praxair was known for its advanced cryogenic systems and PSA nitrogen generators. Today, its legacy technologies continue to influence Linde’s offerings, particularly in North and South America.
Praxair’s expertise in supplying ASUs for metal fabrication and food processing remains relevant, with systems designed for flexibility and low maintenance. As part of Linde, Praxair’s innovations enhance the group’s position as a leading air separation unit supplier.
Praxair’s expertise in supplying ASUs for metal fabrication and food processing remains relevant, with systems designed for flexibility and low maintenance. As part of Linde, Praxair’s innovations enhance the group’s position as a leading air separation unit supplier.
Other Notable Air Separation Unit Suppliers
Beyond the industry giants, several specialized companies contribute to the ASU market:
- Hangzhou Z-Oxygen Intelligent Device Co., Ltd.: Based in China, this supplier offers a range of air separation solutions, including PSA oxygen/nitrogen generators and cryogenic plants, with a focus on international projects.
- Messer Group: A German company, Messer provides ASUs for industries like glass manufacturing and pharmaceuticals, emphasizing compact and efficient designs.
- Taiyo Nippon Sanso Corporation: This Japanese firm excels in high-purity gas production, supplying ASUs for electronics and medical applications in Asia.
These air separation unit suppliers cater to niche markets and regional demands, offering tailored solutions for diverse applications.
Technologies Driving Air Separation Unit Suppliers
The ASU industry is evolving rapidly, with air separation unit suppliers adopting cutting-edge technologies to meet modern demands. Key trends include:
Energy Efficiency
Energy consumption is a significant concern in air separation, particularly for cryogenic processes. Leading suppliers like Linde and Air Liquide are developing ASUs with advanced heat exchangers and compressors to minimize power usage. These innovations reduce operational costs and environmental impact, making energy-efficient ASUs a priority for air separation unit suppliers.
Energy consumption is a significant concern in air separation, particularly for cryogenic processes. Leading suppliers like Linde and Air Liquide are developing ASUs with advanced heat exchangers and compressors to minimize power usage. These innovations reduce operational costs and environmental impact, making energy-efficient ASUs a priority for air separation unit suppliers.
Modular and On-Site Solutions
PSA and membrane-based ASUs are gaining popularity for their portability and ease of installation. Suppliers like Air Products offer modular systems that can be deployed at remote sites, such as mining operations or hospitals. These compact units provide a cost-effective alternative to traditional cryogenic plants, expanding the reach of air separation unit suppliers.
PSA and membrane-based ASUs are gaining popularity for their portability and ease of installation. Suppliers like Air Products offer modular systems that can be deployed at remote sites, such as mining operations or hospitals. These compact units provide a cost-effective alternative to traditional cryogenic plants, expanding the reach of air separation unit suppliers.
Digitalization and Automation
Digital tools are transforming ASU operations. Suppliers are integrating IoT sensors and predictive maintenance systems into their units, enabling real-time monitoring and optimization. Air Liquide’s smart ASU platforms, for example, use data analytics to improve performance, positioning them as forward-thinking air separation unit suppliers.
Digital tools are transforming ASU operations. Suppliers are integrating IoT sensors and predictive maintenance systems into their units, enabling real-time monitoring and optimization. Air Liquide’s smart ASU platforms, for example, use data analytics to improve performance, positioning them as forward-thinking air separation unit suppliers.
Global Applications of Air Separation Units
Air separation unit suppliers serve a wide range of industries, each with unique gas requirements:
- Healthcare: Medical oxygen produced by ASUs is critical for hospitals and emergency response. Suppliers like Air Liquide prioritize high-purity oxygen systems for this sector.
- Metallurgy: Steel and aluminum production rely on oxygen and nitrogen from ASUs. Linde’s large-scale cryogenic plants are widely used in this industry.
- Chemicals and Energy: Nitrogen is essential for inerting in chemical plants, while oxygen supports combustion in energy production. Air Products supplies ASUs for these applications.
- Electronics: High-purity nitrogen from ASUs is used in semiconductor manufacturing. Taiyo Nippon Sanso is a key air separation unit supplier in this field.
Challenges Facing Air Separation Unit Suppliers
Despite their success, air separation unit suppliers face several challenges:
- Environmental Regulations: Stricter emissions standards are pushing suppliers to develop greener ASUs. This includes integrating renewable energy sources and carbon capture technologies.
- Cost Pressures: High capital costs for large-scale ASUs can deter smaller clients. Suppliers are addressing this by offering leased or modular systems.
- Competition: The market is highly competitive, with regional players challenging global giants. Suppliers must differentiate through innovation and customer service.
The Future of Air Separation Unit Suppliers
The ASU industry is poised for growth, driven by rising demand for industrial gases in developing economies and advancements in green technologies. Air separation unit suppliers are investing in sustainable solutions, such as hydrogen-compatible ASUs and low-carbon production methods. Companies like Linde and Air Products are also exploring AI-driven designs to enhance ASU performance.
As industries continue to evolve, air separation unit suppliers will remain at the forefront, delivering the gases that power global progress. Whether through massive cryogenic plants or compact PSA systems, these suppliers are shaping a future where high-purity gases are accessible and sustainable.
Conclusion
Air separation unit suppliers like Linde, Air Liquide, and Air Products lead the industry with innovative technologies and global expertise. Their contributions span healthcare, manufacturing, and energy, meeting diverse needs with efficiency and precision. As the demand for industrial gases grows, these air separation unit suppliers will continue to drive advancements, ensuring a steady supply of oxygen, nitrogen, and argon for a rapidly changing world.